Metal Injection Moulding: Revolutionizing Metal Manufacturing
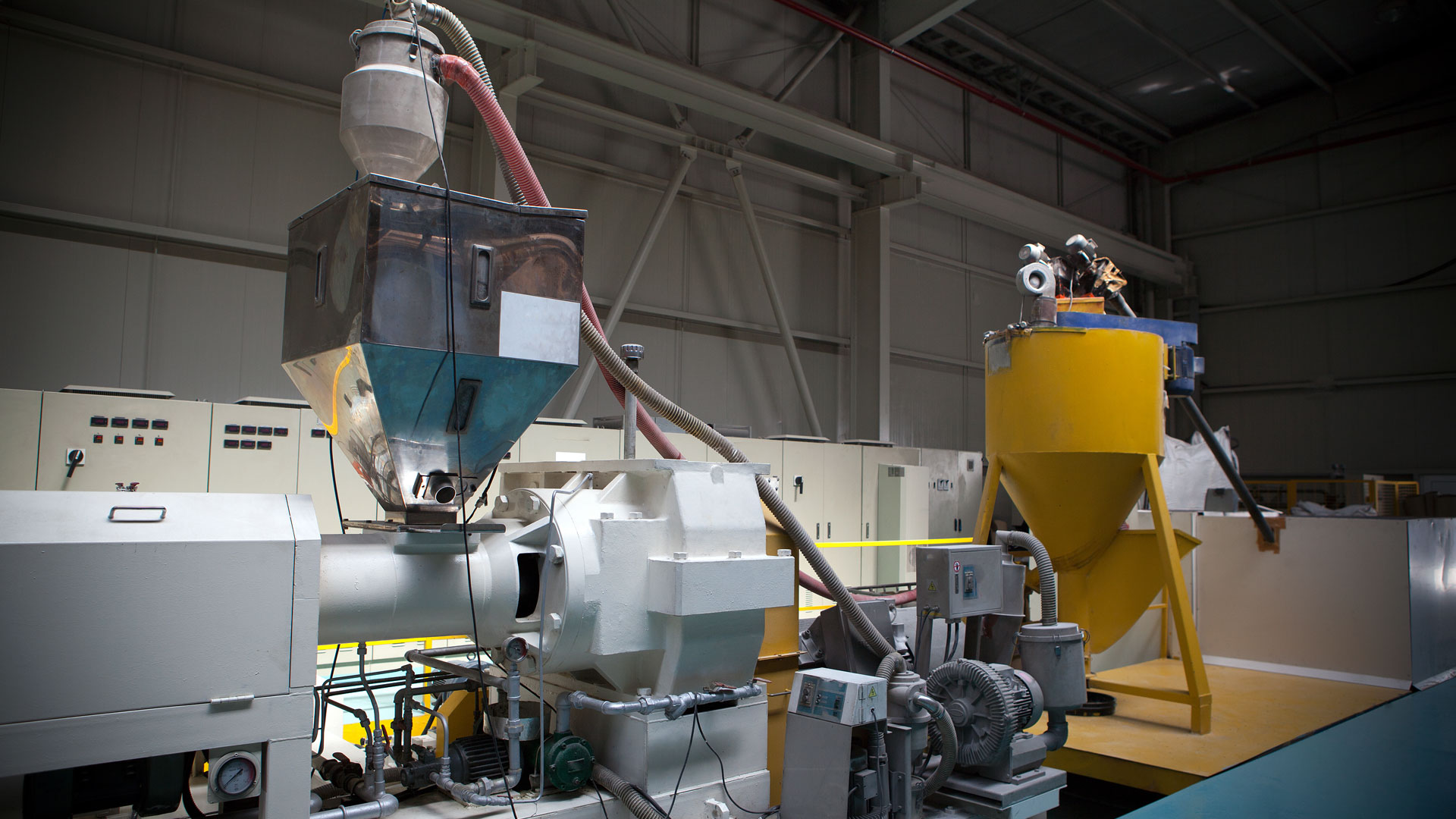
What is Metal Injection Moulding (MIM)?
Metal injection moulding (MIM) is a revolutionary manufacturing process that combines the precision and efficiency of plastic injection moulding with the strength and durability of metal. This innovative technique has gained significant traction in recent years, enabling the production of intricate metal components that were once challenging or impossible to achieve using traditional methods.
A Glimpse into MIM Technology
Developed in the 1970s, MIM has emerged as a game-changer for various industries. The process involves blending fine metal powders with a thermoplastic binder to create a feedstock material. This feedstock behaves similarly to molten plastic, allowing it to be injected into intricate moulds under high pressure. After shaping, the binder is removed through a thermal debinding process, leaving a fragile metal skeleton behind. Finally, the metal part undergoes sintering, a high-temperature process that densifies the metal powder and achieves its final strength and properties.
The Advantages of Metal Injection Moulding
MIM offers a multitude of benefits compared to traditional metalworking methods:
Complex Part Production: MIM excels at producing intricate metal parts with tight tolerances and complex geometries, which might be difficult or expensive to achieve through conventional machining or casting techniques.
Near-Net-Shape Manufacturing: MIM minimizes the need for extensive post-processing, reducing material waste and production costs.
High Precision and Repeatability: The controlled nature of the injection moulding process allows for high dimensional accuracy and consistent part quality across large production runs.
Material Versatility: MIM can work with a wide range of metal powders, including stainless steel, steel alloys, copper, and even exotic materials like titanium.
Cost-Effectiveness: For high-volume production of complex parts, MIM can be a cost-effective alternative to traditional methods, especially when considering reduced machining needs and material waste.
Limitations of MIM
While offering numerous advantages, MIM also has certain limitations to consider:
Part Size Restrictions: Due to the debinding and sintering processes, there are limitations on the maximum size of parts that can be produced through MIM.
High Initial Tooling Costs: The development of moulds for MIM can be expensive, similar to other injection moulding processes.
Material Properties: MIM parts may not always achieve the same level of mechanical strength compared to parts produced through traditional methods like forging or machining.
Applications of Metal Injection Moulding
The unique capabilities of MIM make it suitable for a wide range of applications across various industries:
Automotive: Gears, engine components, fuel system parts, transmission components
Medical Devices: Surgical instruments, implants, dental prosthetics
Electronics: Connectors, heat sinks, housings for electronic components
Aerospace: Aerospace components, fuel system components, lightweight structural parts
Consumer Goods: Watch components, lock components, appliance parts
Shilpan Steelcast: Your Partner for Metal Injection Molding in India.
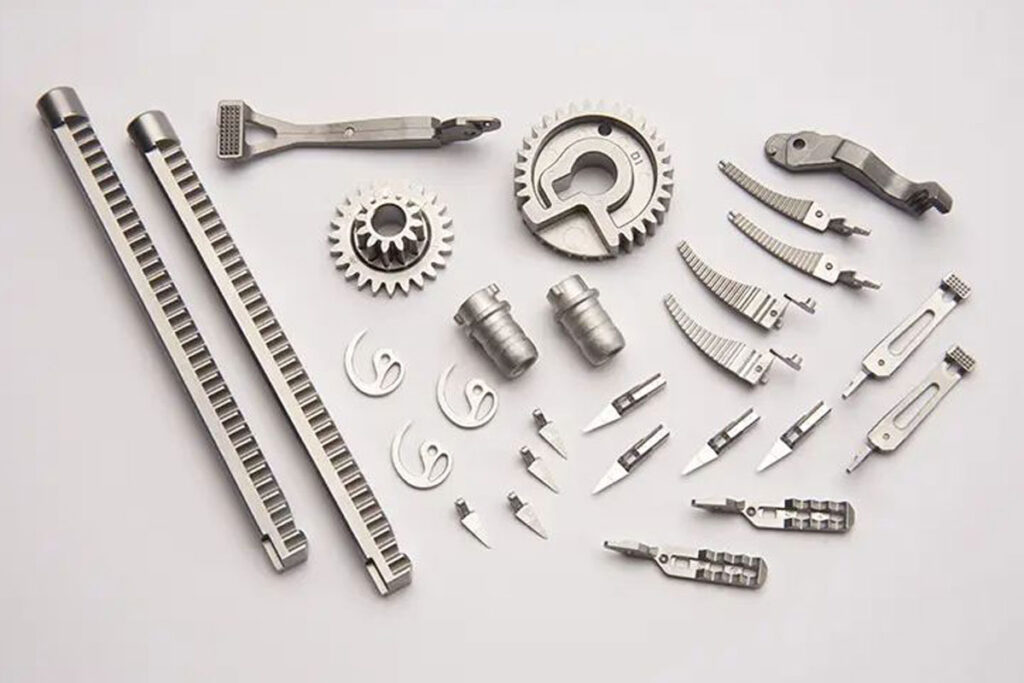
Shilpan Steelcast is a leading provider of metal injection moulding services in India. We possess the expertise and advanced technology to deliver high-quality MIM parts for diverse requirements. From material selection and mould design to debinding, sintering, and finishing, Shilpan Steelcast ensures a seamless and efficient production process.
Metal injection moulding is a revolutionary and versatile technology that is transforming metal manufacturing. With its ability to produce complex, near-net-shape parts with high precision, MIM is a valuable option for various industries. By understanding the process, its advantages and limitations, and the expertise offered by Shilpan Steelcast, businesses can leverage MIM to enhance their production capabilities and achieve success.
Ready to explore the potential of metal injection moulding for your projects?
Contact Shilpan Steelcast today to discuss your metal injection moulding requirements and discover how we can help you achieve your manufacturing goals.