Metal Stamping: Your Solution for Efficient Manufacturing
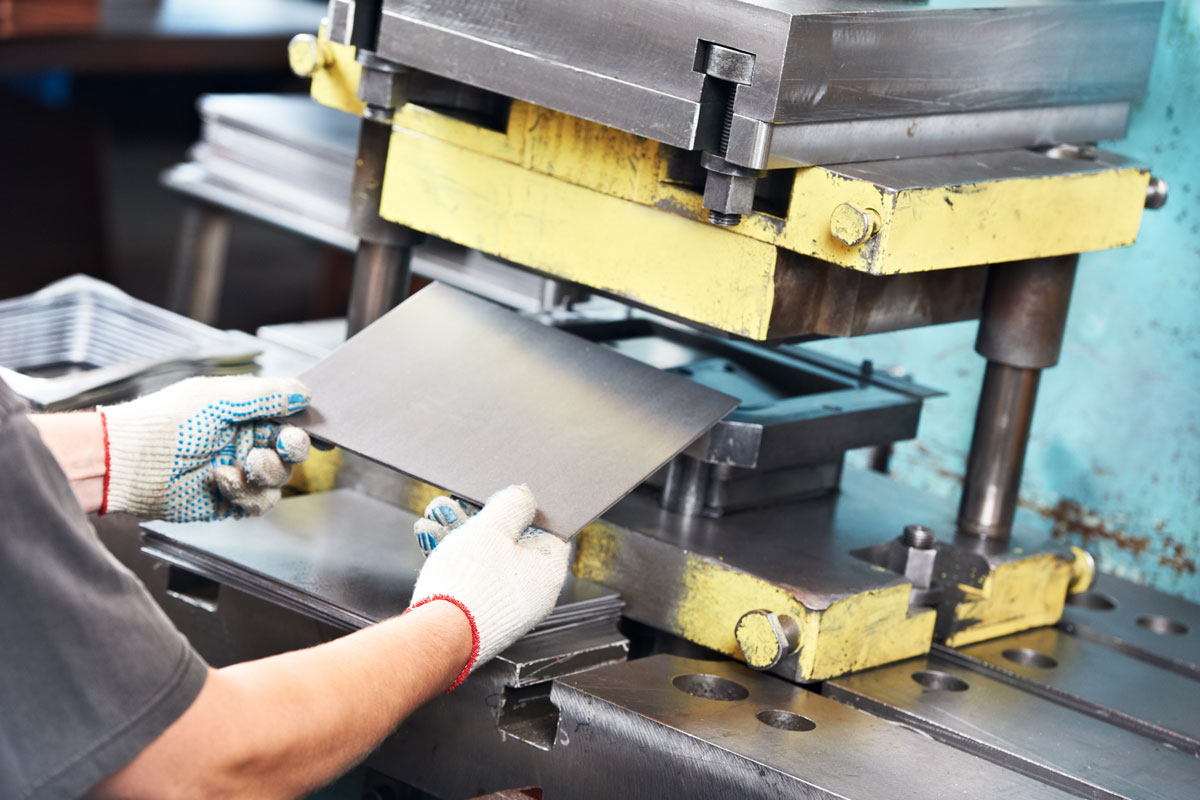
What is Metal Stamping?
Metal stamping is a versatile manufacturing process that involves shaping metal sheets into desired forms using pressure and a die. The process typically involves three main steps: cutting, forming, and finishing. In the cutting step, the metal sheet is cut into the desired shape. The forming step involves deforming the metal sheet using a die to create the desired shape or features. Finally, the finishing step involves removing any excess material, smoothing the edges, and adding any necessary surface treatments. This technique is widely employed across various industries due to its efficiency, precision, and ability to produce complex parts in high volumes.
A Brief History of Metal Stamping
Metal stamping has been used for centuries, dating back to ancient civilizations. Early forms of metal stamping involved hammering metal into simple shapes using rudimentary tools. Over time, advancements in technology led to the development of more sophisticated stamping presses and die, enabling the production of intricate and complex parts.
Types of Metal Stamping
There are several types of metal stamping processes, each with its unique applications and characteristics:
- Blanking: Cutting metal sheets into desired shapes. Examples: Automotive body panels, electrical enclosures
- Bending: Forming metal sheets into angles or curves. Examples: Brackets, brackets, automotive chassis components
- Drawing: Deepening metal sheets to create hollow shapes. Examples: Can bodies, cookware, automotive components
- Forming: Shaping metal sheets into complex three-dimensional forms. Examples: Automotive body panels, kitchen appliances
- Coining: Producing intricate details and patterns on metal surfaces. Examples: Coins, decorative items
- Punching: Creating holes or other openings in metal sheets. Examples: Holes in sheet metal, electrical connectors
The Metal Stamping Process
The metal stamping process typically involves the following steps:
- Die Design and Fabrication: A hardened steel die is designed and manufactured to match the desired shape of the part. The die’s design must consider factors such as material properties, part complexity, and production volume. Shilpan Steelcast specializes in designing and fabricating complex dies to meet the specific requirements of clients.
- Material Preparation: Metal sheets of the appropriate thickness and material are prepared for stamping. Shilpan Steelcast has expertise in handling a wide range of metals, including stainless steel, aluminum, brass, and copper.
- Press Operation: The metal sheet is placed between the upper and lower dies of a stamping press. The press applies pressure, forcing the metal to conform to the die shape. Shilpan Steelcast uses state-of-the-art stamping presses that can handle various part sizes and complexities.
- Finishing: The stamped part may undergo additional finishing processes such as trimming, deburring, polishing, or coating. Shilpan Steelcast offers a range of finishing services to ensure the final product meets the desired specifications.
Advantages of Metal Stamping
Metal stamping offers numerous advantages that make it a popular manufacturing method:
High Production Rates: It can produce large quantities of parts efficiently, reducing manufacturing costs and lead times.
Precision and Accuracy: The process can achieve high levels of precision and accuracy in part dimensions, ensuring consistency and quality.
Cost-Effectiveness: It is often more cost-effective compared to other manufacturing methods, especially for high-volume production.
Versatility: It can be used to produce a wide range of parts, from simple shapes to complex components.
Material Efficiency: Metal stamping minimizes material waste, leading to improved sustainability and cost savings.
Limitations
While this metal manufacturing process offers numerous benefits, it also has certain limitations:
- Part Complexity: Some parts may be too complex or require intricate details that are difficult to achieve through stamping. In such cases, other manufacturing methods may be more suitable.
- Material Limitations: Certain materials may not be suitable for stamping due to their properties or thickness. For example, very brittle or hard materials may be challenging to stamp.
- Tooling Costs: The initial investment in dies can be significant, especially for complex parts. However, the cost can be offset by the high production volumes and efficiency achieved through stamping.
Applications
Metal stamping is widely used in various industries, including:
- Automotive: Body panels, engine components, suspension parts
- Electronics: Casing, brackets, connectors
- Consumer Goods: Appliances, toys, hardware
- Construction: Building components, fasteners
- Industrial Machinery: Parts for machinery and equipment
Shilpan Steelcast’s Expertise
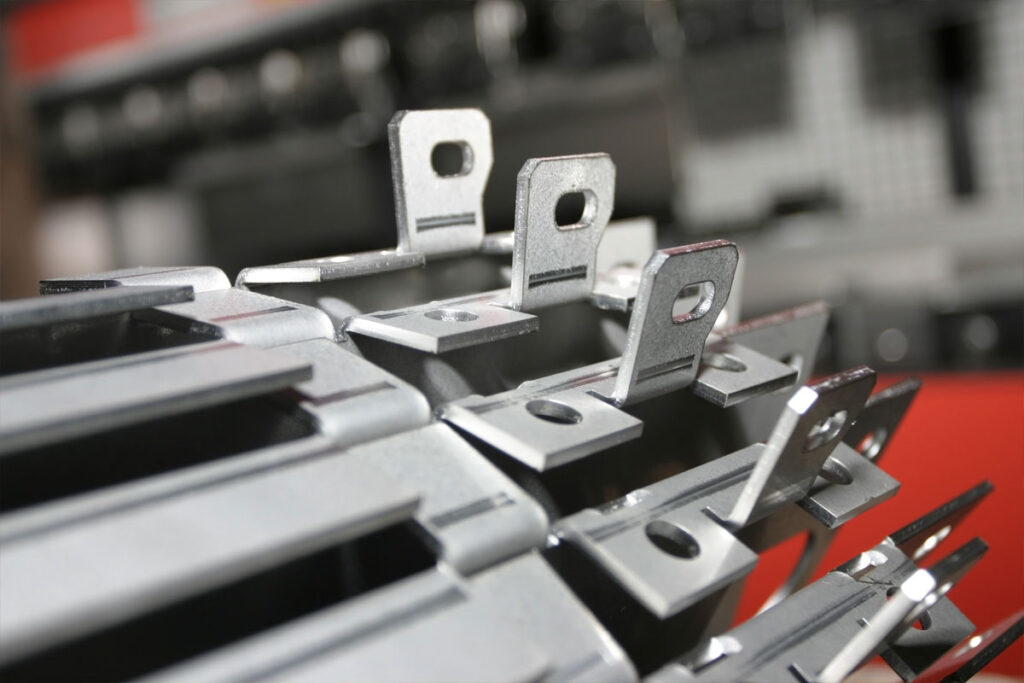
Shilpan Steelcast is a leading provider of metal stamping services in India, offering a wide range of capabilities and expertise. With state-of-the-art equipment and skilled professionals, we can deliver high-quality metal stamped parts to meet the demanding requirements of various industries.
Some of the key areas of expertise at Shilpan Steelcast include:
- Complex part design and fabrication
- High-volume production capabilities
- Precision stamping and tolerance control
- Advanced finishing techniques
- Material selection and processing
Metal stamping is a versatile and efficient manufacturing process that offers numerous benefits, including high production rates, precision, cost-effectiveness, and versatility. By understanding the different types of stamping, the process involved, and its advantages and limitations, businesses can make informed decisions about incorporating the process into their production strategies. Shilpan Steelcast, with its years of manufacturing experience and expertise, is well-positioned to deliver high-quality metal stamped parts that meet the demanding needs of various industries.
Ready to elevate your manufacturing processes with metal stamping? Contact Shilpan Steelcast today to discuss your project requirements and explore how we can help you achieve your goals.