Metal Casting vs. Metal Forging: Choosing the Right Path for Your Metal Component Needs
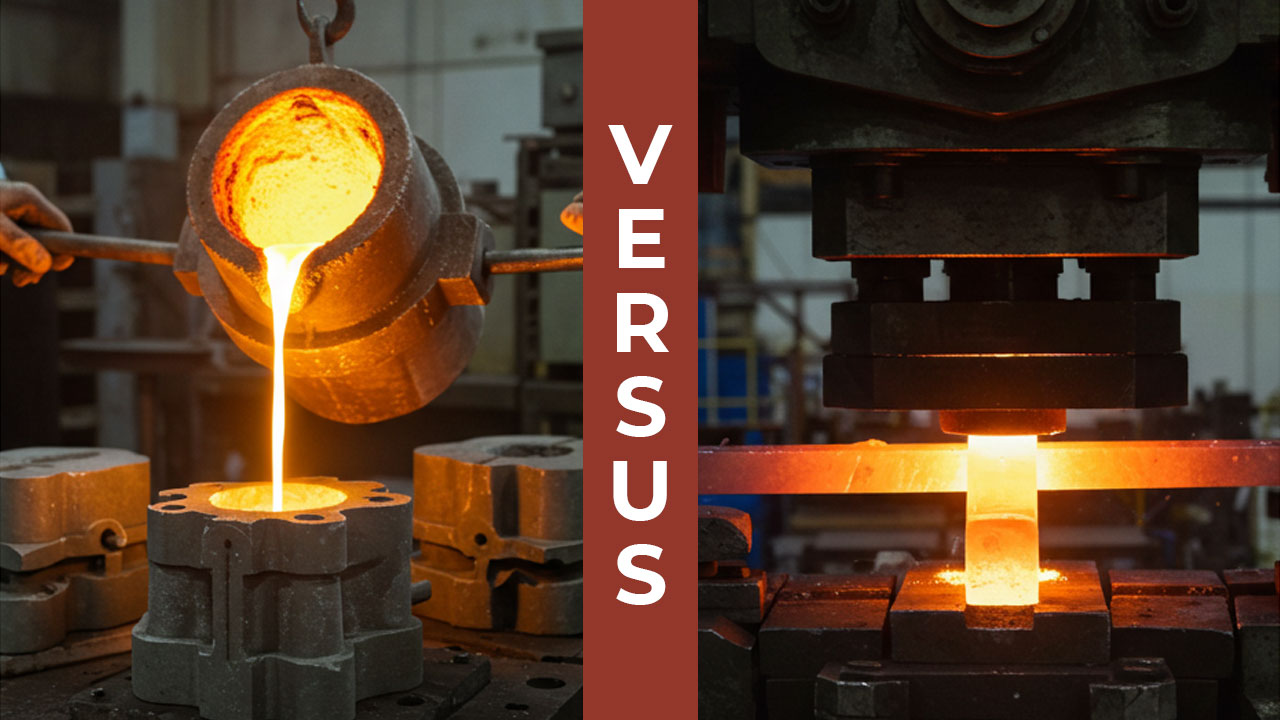
In the realm of metalworking, two primary processes stand out for shaping raw metal into functional components: metal casting and metal forging. While both achieve the fundamental goal of creating metal parts, they employ distinct methodologies, resulting in components with different characteristics and suitability for various industrial applications. Understanding the nuances of each process is essential for engineers and procurement teams to make informed decisions.
Decoding Metal Casting: Shaping Metal Through Molten Form
Metal casting involves the fundamental step of melting metal and then introducing this molten material into a mould – a cavity meticulously designed to replicate the desired final shape. As the molten metal cools and solidifies within the mold, it assumes the mold’s form. Once completely solid, the newly formed metal part, known as a casting, is extracted.
Key Attributes of Metal Casting
- Shape Versatility: Casting shines when producing intricate and complex geometries, including those with internal passages and intricate detailing that would be challenging or impossible with forging.
- Size Adaptability: From miniature, highly detailed components to massive industrial parts, casting can handle an impressive spectrum of sizes.
- Material Diversity: The casting process is compatible with a vast array of metals and alloys, offering greater flexibility in material selection, including those with lower forgeability.
- Economic Advantage for Complexity: For designs featuring significant complexity, casting often presents a more cost-effective manufacturing route compared to the tooling and labor involved in complex forging.
Exploring Common Metal Casting Techniques
- Investment Casting (Lost-Wax Process): This sophisticated technique employs wax patterns encased in a ceramic shell to produce castings with remarkable accuracy and intricate details.
- Die Casting: Molten metal is forcefully injected into reusable metal molds (dies) under high pressure, yielding parts with exceptional dimensional precision and smooth surface finishes.
- Sand Casting: A time-honored and economical method utilizing molds made from sand mixtures.
Unveiling Metal Forging: Shaping Metal Through Force
In contrast to casting, metal forging involves shaping metal in its solid state through the application of localized compressive forces. This force is typically delivered through hammering, pressing, or rolling operations. The key distinction here is that the metal never reaches its molten state.
Key Attributes of Metal Forging
- Enhanced Strength and Integrity: The compressive forces applied during forging refine the metal’s internal grain structure, leading to superior strength, increased toughness, and enhanced resistance to fatigue and impact.
- Improved Structural Reliability: The forging process minimizes internal voids and discontinuities, resulting in components with greater structural integrity and reliability, especially under stress.
- Exceptional Durability: Forged parts inherently possess greater durability and a longer service life due to their dense and refined microstructure.
- Ideal for High-Stress Applications: When components are destined for demanding applications involving significant loads or impacts, forging is often the preferred choice.
Common Metal Forging Techniques
- Open Die Forging: The metal is shaped between flat or simple contour dies, offering flexibility for producing a range of shapes and sizes, particularly larger components.
- Closed Die Forging (Impression Die Forging): The metal is shaped within precisely machined dies that impart the final desired form, resulting in high accuracy and repeatability.
- Rolled Ring Forging: A specialized process used to create seamless rings with exceptional strength and uniform grain flow, ideal for applications like bearings and flanges.
Metal Casting vs. Metal Forging: A Comparative Overview
Feature | Metal Casting | Metal Forging |
---|---|---|
Shape Complexity | Excellent for intricate designs and complex internal features. | Best suited for simpler overall shapes, though closed-die forging can achieve some complexity. |
Size Capabilities | Highly versatile, accommodating a very wide spectrum of component sizes. | Can handle a broad range of sizes, but very large, intricate parts may favor casting. |
Mechanical Properties | Generally exhibits lower strength and fatigue resistance compared to forgings. | Delivers superior strength, toughness, impact resistance, and fatigue life. |
Dimensional Precision | Can achieve good accuracy, particularly with methods like die and investment casting. | Typically offers high dimensional accuracy, especially with closed-die and precision forging. |
Material Suitability | Compatible with a broad range of metals and alloys, offering greater material flexibility. | Some limitations in alloy selection may exist due to forgeability requirements. |
Production Economics | Can be more economical for complex shapes and lower to medium production volumes. | Often more cost-effective for medium to high production volumes of simpler to moderately complex parts. |
Internal Structure | Gears, shafts, connecting rods, aerospace structural components, and high-stress fasteners. | Results in a dense, refined, and continuous grain flow, enhancing structural integrity. |
Typical Applications | Engine blocks, pump housings, impellers, complex brackets, decorative parts. | Gears, shafts, connecting rods, aerospace structural components, high-stress fasteners. |
Making the Right Choice for Your Industrial Needs
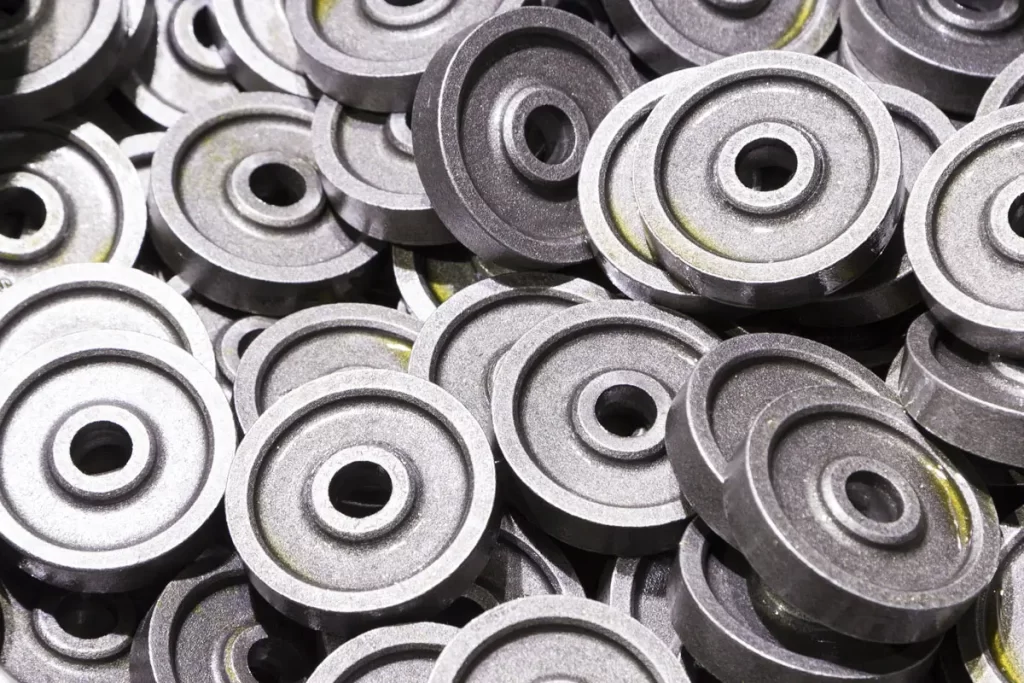
The decision between metal casting and metal forging hinges on a careful evaluation of your specific application requirements. Consider the following critical factors:
- Complexity of the Part Design: Intricate shapes often favor casting.
- Required Mechanical Properties: High-stress applications typically demand the superior strength of forgings.
- Production Volume: The economics of each process can shift depending on the number of parts needed.
- Material Specifications: Certain alloys may be more readily cast than forged, or vice versa.
- Budgetary Constraints: Initial tooling costs and per-part costs can vary significantly between the two processes.
By thoroughly analyzing these aspects, you can determine whether the design flexibility and material versatility of metal casting or the enhanced strength and durability of metal forging is the optimal path for manufacturing your critical metal components.
Considering Metal Component Manufacturing?
At Shilpan Steelcast, we offer a comprehensive range of metal manufacturing solutions, including both precision metal casting and advanced forging capabilities. Our experienced team can work with you to understand your specific needs and recommend the most efficient and effective process for your industrial applications.
We offer a range of value-added services, including:
- In-house precision machining for finished parts
- Assembly services
- Advanced quality control and testing facilities
- Commitment to international standards including ISO 9001:2015, IATF 16949:2016, PED, and AD 2000
Contact us today to discuss your project requirements and leverage our expertise in metal casting and forging.