Why Investment Casting is Ideal for Complex Valve and Pump Components
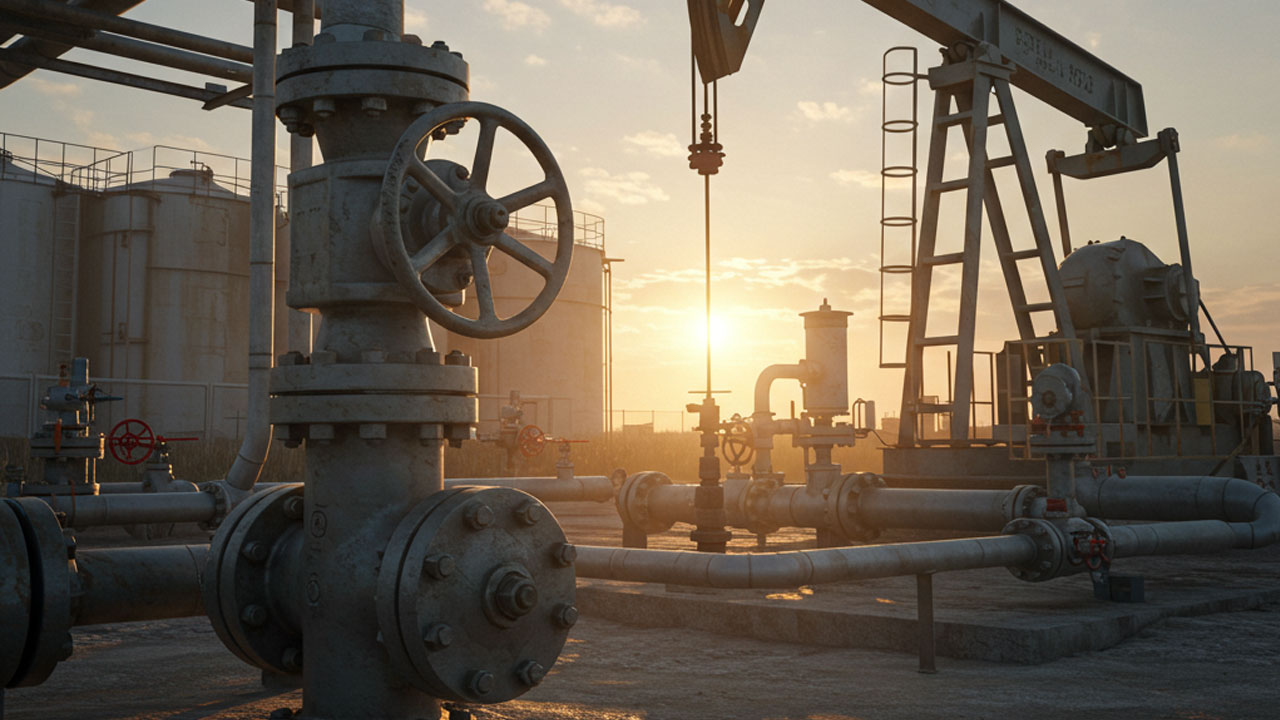
In the world of industrial manufacturing, few components face the demanding operating conditions that valves and pumps do. From controlling fluid flow in oil and gas pipelines to ensuring precision dosing in pharmaceutical applications, these parts require outstanding mechanical strength, tight tolerances, and long-term durability. For manufacturers seeking to meet these performance standards while optimizing costs, investment casting has emerged as the ideal solution—especially for complex valve and pump components.
The Challenge of Manufacturing Valve and Pump Components
Valves and pumps are critical components across a wide range of industries, including oil & gas, power generation, chemical processing, food & beverage, and water treatment. These components often feature:
- Complex geometries such as flow passages, internal cavities, or intricate contours.
- Demanding material requirements for corrosion resistance, thermal stability, or strength under high pressure.
- Tight dimensional tolerances necessary for proper sealing and flow control.
- Smooth surface finishes to reduce turbulence and material buildup.
Traditional manufacturing methods such as sand casting, forging, or machining from solid billet often struggle to meet these requirements cost-effectively, especially when it comes to complexity and precision.
Why Investment Casting Excels for Valve and Pump Components
Investment casting—also known as lost-wax casting—is a precision manufacturing process capable of producing near-net-shape parts with excellent surface finish, complex details, and a wide variety of alloys.
Here’s why it’s a perfect fit for valve and pump component manufacturing:
1. Complex Geometries with Ease
Investment casting can produce intricate internal and external features that are difficult or impossible to achieve with forging or sand casting. This includes:
- Flow channels
- Thin walls
- Curved vanes
- Tight radius transitions
This design freedom significantly reduces the need for secondary machining or assembly.
2. Superior Surface Finish
Valve and pump components benefit from smoother surfaces to ensure efficient flow and reduce wear. Investment casting offers excellent surface finishes—typically Ra 3.2–6.3 µm—right out of the mold.
3. Material Versatility
Investment casting supports a wide range of alloys tailored to various industrial needs, including:
- Stainless steels (CF8M, CF3M, etc.) for corrosion resistance
- Duplex and super duplex steels for strength and chemical resistance
- Nickel-based alloys for high-temperature applications
This ensures the right material is selected for each specific use case.
4. Dimensional Accuracy
Tight tolerances (±0.1 mm or better, depending on size) reduce the need for post-casting machining and improve overall quality and consistency, critical for sealing and flow control in valves and pumps.
5. Cost-Effectiveness at Medium Volumes
While not suited for very low or very high volumes, investment casting is ideal for medium production runs. Tooling costs are offset by savings in machining, material waste, and assembly complexity.
Common Valve and Pump Components Made via Investment Casting
Many critical components used in pump and valve assemblies are ideally suited for investment casting, such as:
- Valve bodies and bonnets
- Pump impellers and housings
- Discs, plugs, and seats
- Flow control vanes and guides
- Inlet/outlet fittings and covers
Each of these parts benefits from the precision, strength, and design freedom of the investment casting process.
Investment Casting vs. Other Manufacturing Methods
Criteria | Investment Casting | Forging | Sand Casting | Machining from Solid |
---|---|---|---|---|
Complexity | Excellent | Limited | Moderate | High (but expensive) |
Tolerances | High | Very high | Low | Very high |
Surface Finish | Excellent | Good | Poor | Excellent |
Material Waste | Low | Low | Moderate | High |
Cost at Medium Volume | Cost-effective | Costly | Moderate | Expensive |
Shilpan Steelcast’s Expertise in Valve and Pump Castings
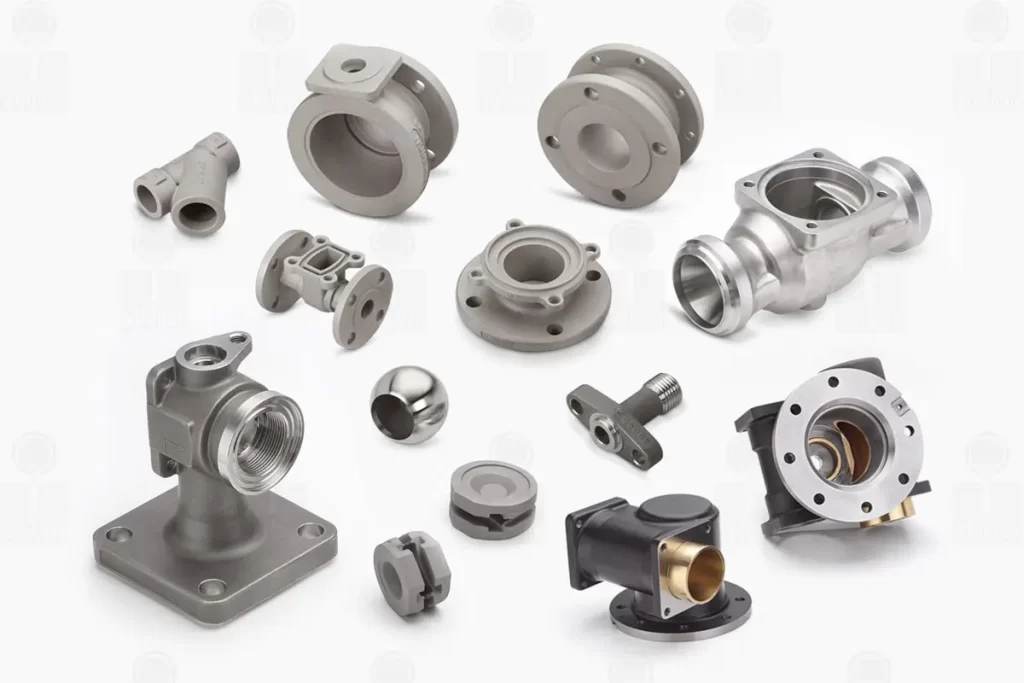
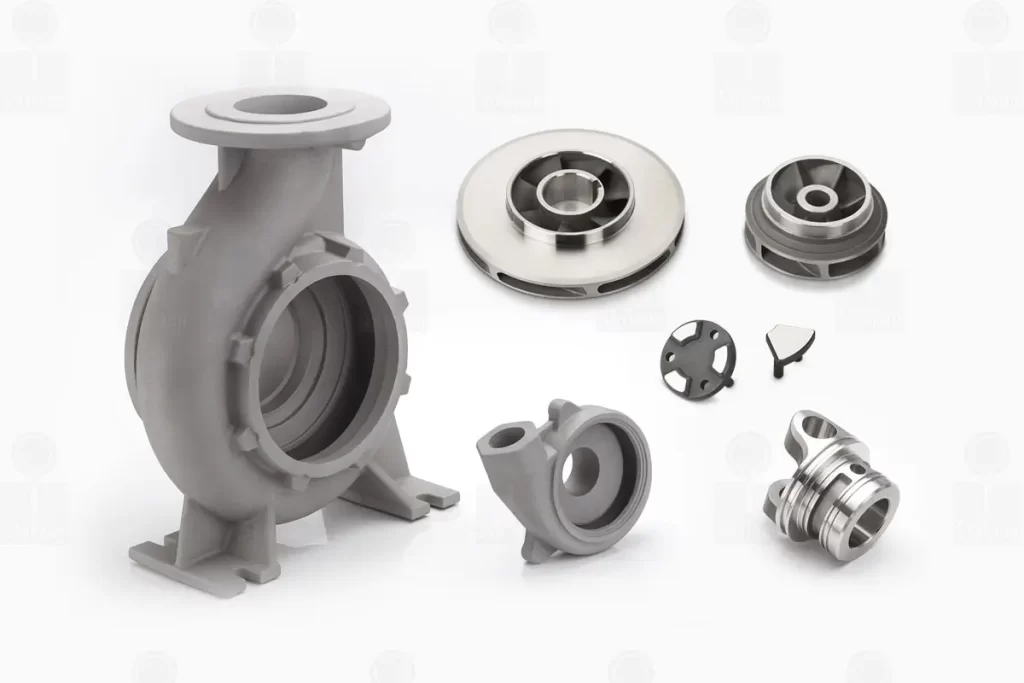
As one of India’s leading investment casting manufacturers, Shilpan Steelcast has developed deep expertise in producing high-performance components for valve and pump manufacturers worldwide.
Highlights of Shilpan Steelcast’s Capabilities:
- Modern Investment Casting Foundry in Rajkot: Located in India’s renowned investment casting hub, our 200,000 sq. ft. facility integrates advanced casting technologies and process automation to deliver consistent quality.
- Material Capabilities: Expertise in casting a broad spectrum of stainless steels, duplex, carbon steels, and specialty alloys used in fluid handling applications.
- In-House CNC Machining: Our in-house machining division ensures we can meet tight tolerances and provide ready-to-install components, saving time and cost for our clients.
- Assembly Services: Shilpan also offers assembly services for complex pump and valve assemblies, delivering even greater value and reducing supply chain complexity for OEMs.
- Quality Assurance: With certifications including ISO 9001:2015, IATF 16949:2016, PED 2014/68/EU, and AD 2000 – Merkblatt W0, we follow rigorous inspection and testing protocols to ensure reliability.
Conclusion
In industries where performance, reliability, and precision matter most, investment casting proves to be the ideal manufacturing method for complex valve and pump components. It enables intricate design, material flexibility, and cost efficiency without compromising quality.
With its world-class foundry, in-house machining, and engineering support, Shilpan Steelcast is a trusted partner for global OEMs in fluid control and handling applications. Whether you’re designing a high-performance valve or a critical pump component, Shilpan is equipped to turn your vision into reality, with precision and reliability at its core.
Ready to discuss your next valve or pump casting project?
Get in touch with Shilpan Steelcast today.