Innovative Applications of Investment Casting in the Automotive Industry
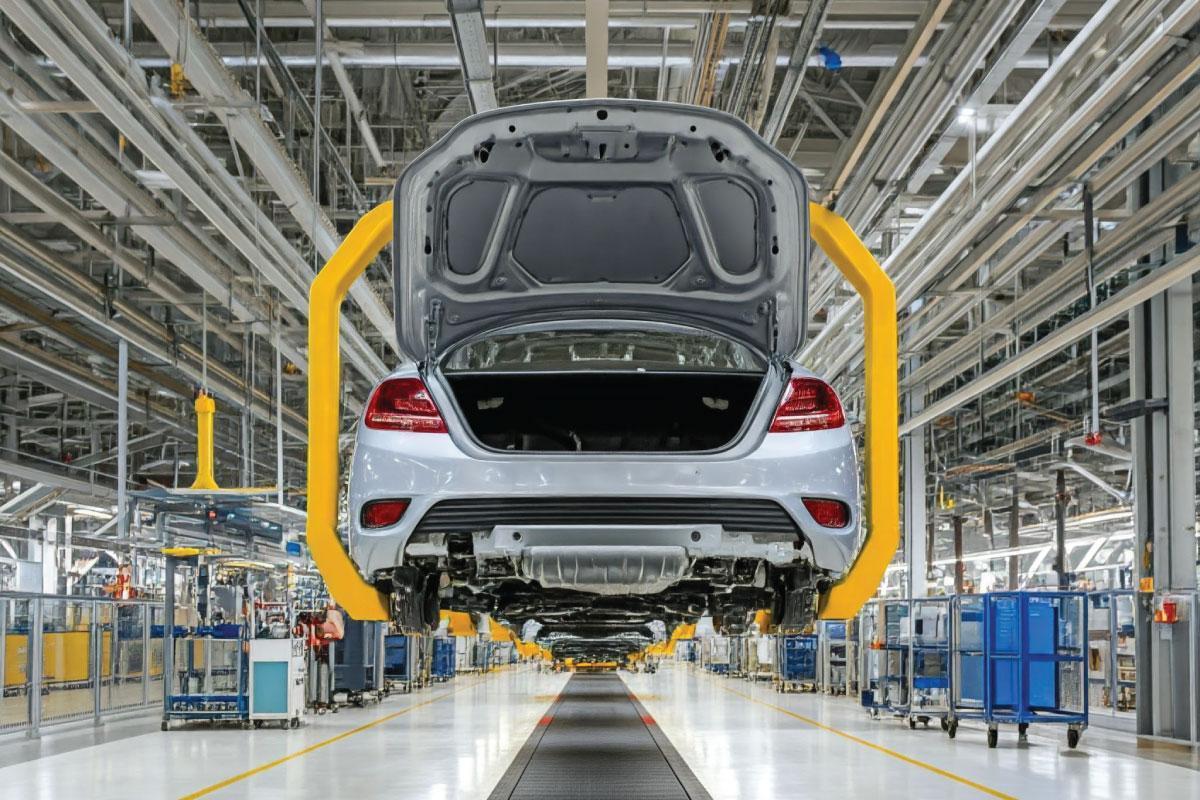
Investment casting, also known as precision casting or lost-wax casting or Feinguss in German, has transformed the way manufacturers approach complex, high-precision parts production. While this method is widely used across multiple sectors, its impact on the automotive industry is especially significant. As modern vehicles require components that are lightweight, durable, and designed with intricate geometries, investment casting is playing a crucial role in enabling these advancements. In this article, we explore how investment casting is driving innovation in the automotive industry, contributing to improved vehicle performance, fuel efficiency, and design flexibility.
Why Investment Casting is Ideal for the Automotive Industry
The automotive industry demands manufacturing processes that can deliver high-quality, consistent results across large production runs. Investment casting meets these requirements and offers additional advantages that align with the automotive sector’s priorities:
- High Precision and Complexity: Investment casting allows for the creation of complex and intricate shapes, which is ideal for automotive components that must fit within tight design tolerances. This process ensures that every cast part meets precise specifications, reducing the need for costly secondary machining.
- Material Versatility: Investment casting supports a broad range of metal alloys, including high-strength, heat-resistant materials. This versatility allows automotive manufacturers to select materials that provide durability and performance in demanding environments, such as under-the-hood components or high-stress suspension systems.
- Reduced Weight: Weight reduction is a key focus in automotive manufacturing, as lighter vehicles offer better fuel efficiency. Investment casting enables the production of lightweight parts with thin walls and complex shapes, reducing the overall weight of the vehicle without compromising strength or integrity.
- Cost Efficiency in Mass Production: Investment casting minimizes material waste and offers repeatable precision, making it an efficient process for producing large volumes of parts. This results in significant cost savings, especially for high-volume automotive applications.
Key Automotive Components Made Using Investment Casting
Investment casting has enabled automotive manufacturers to produce a wide range of components with enhanced quality and performance. Some key automotive parts that benefit from investment casting include:
- Engine Components: Components like turbine wheels, impellers, and exhaust manifolds are often made using investment casting due to their need for precise geometries and heat resistance. Investment casting ensures these parts maintain their integrity under extreme temperatures and stresses.
- Transmission Systems: Precision gears, clutch components, and housings are crucial for smooth and efficient transmission operation. Investment casting provides the high dimensional accuracy required for these parts, resulting in seamless power transfer and minimized wear.
- Suspension Parts: Suspension systems rely on components like control arms, knuckles, and brackets that must be both lightweight and durable. Investment casting supports the creation of these complex shapes, helping manufacturers achieve strength without unnecessary weight.
- Fuel and Exhaust Systems: Investment casting is often used to produce parts like turbocharger housings, catalytic converter bodies, and exhaust manifolds. These components need to withstand extreme temperatures and corrosive environments, and investment casting provides the necessary durability and precision.
- Safety-Critical Components: Brake callipers, ABS housings, and other safety-critical parts require exceptional reliability and precision. Investment casting ensures these components meet stringent safety standards, enhancing vehicle performance and occupant safety.
Benefits of Investment Casting in the Automotive Innovation
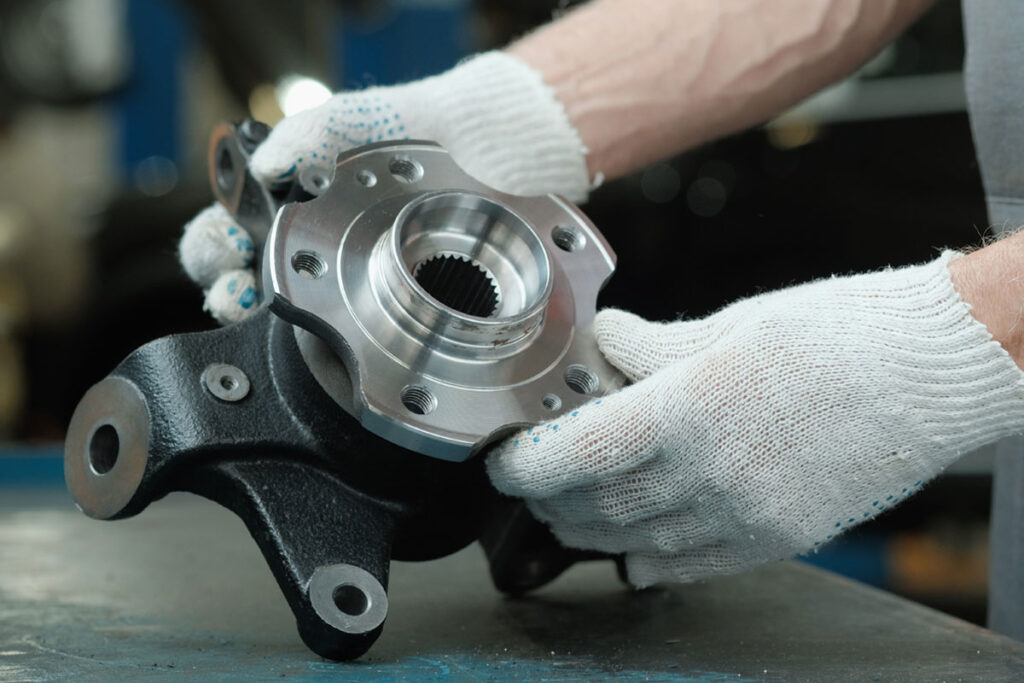
Investment casting offers numerous advantages that support ongoing innovation in the automotive industry:
- Weight Reduction for Fuel Efficiency: By enabling the production of thin-walled, complex components, investment casting helps automotive manufacturers reduce the weight of their vehicles. Lighter vehicles consume less fuel, aligning with the industry’s goals for increased fuel efficiency and reduced emissions.
- Enhanced Design Freedom: Investment casting allows engineers to experiment with innovative designs that may be challenging to achieve through other manufacturing processes. This design freedom supports the development of parts that enhance vehicle aesthetics, functionality, and performance.
- Improved Performance and Durability: The use of high-performance alloys in investment casting leads to components that perform reliably under harsh conditions, such as high temperatures and mechanical stress. This durability is essential for components that experience constant wear, such as engine and suspension parts.
- Cost Savings on Assembly and Machining: Investment casting produces near-net-shape parts, which reduces or eliminates the need for secondary machining. This not only cuts production costs but also minimizes material waste, contributing to sustainable manufacturing practices.
Future of Investment Casting in the Automotive Industry
As the automotive industry evolves, the role of investment casting continues to expand, especially with trends like electric vehicles (EVs) and autonomous driving:
- Electric Vehicles (EVs): Investment casting is ideal for producing lightweight components essential for EV efficiency, such as motor housings and battery support structures. The ability to cast thin-walled, high-strength parts helps extend EV range and reduce energy consumption.
- Sustainability in Manufacturing: Investment casting’s efficiency in material usage aligns with the automotive industry’s shift towards sustainable manufacturing practices. The reduced need for machining and the minimized waste make it an eco-friendly process.
- Autonomous Vehicle Components: Autonomous vehicles require precise, high-quality components for sensors, control systems, and other critical technologies. Investment casting’s precision and quality make it well-suited for producing these components, supporting the growth of autonomous technology in the automotive market.
Shilpan Steelcast’s Expertise in Automotive Investment Casting
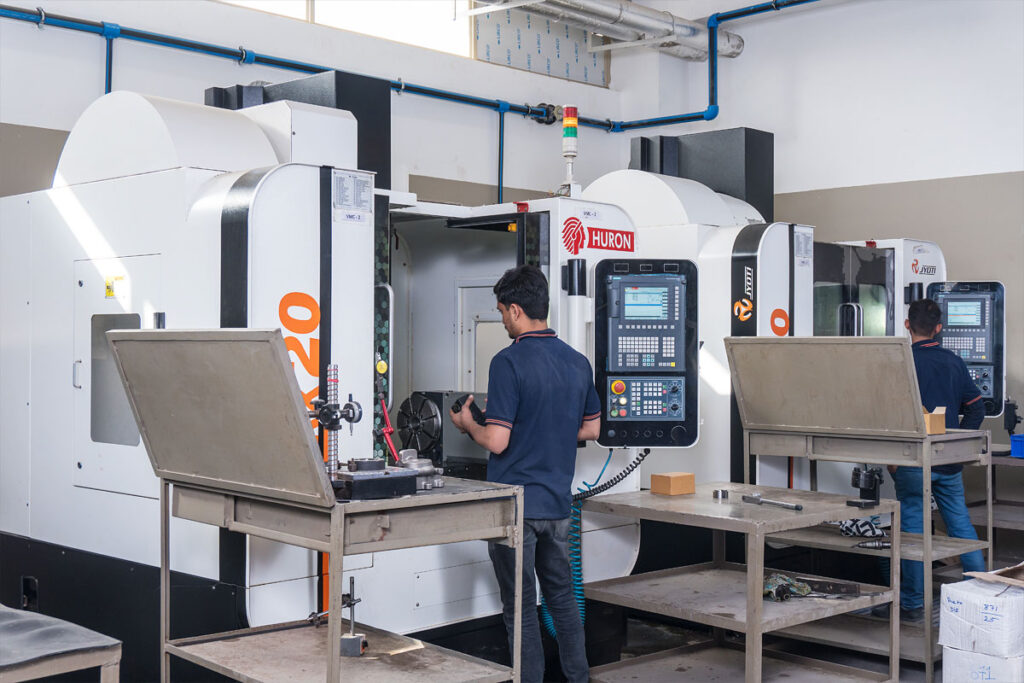
Shilpan Steelcast has established itself as a trusted provider of high-quality investment castings, with a specialized focus on the automotive industry. Our facility, located in Rajkot, India—a renowned hub for investment casting—leverages cutting-edge technology and advanced manufacturing practices to meet the demanding requirements of automotive clients worldwide.
In-House Precision Machining Facility
In addition to our advanced investment casting capabilities, Shilpan Steelcast offers an in-house precision machining facility to manufacture precision machined components. This enables us to provide complete, ready-to-use automotive parts with exceptional dimensional accuracy. By offering both casting and machining under one roof, we streamline the production process, reduce lead times, and maintain rigorous quality standards from start to finish.
IATF 16949:2016 Certified
Shilpan Steelcast holds the prestigious IATF 16949:2016 certification, a globally recognized quality standard for the automotive industry. This certification underscores our commitment to maintaining stringent quality management practices, traceability, and continuous improvement, ensuring that our cast and machined components consistently meet the highest automotive standards.
Advanced Facilities
Our investment casting facility features cutting-edge equipment, including Robotic Shell Room Automation, HMI-controlled wax injection presses, and Rotary Hearth Shell Baking Furnace, ensuring precision and consistency in every casting. Our Robotic Metal Pouring Automation—a pioneering feature in India—further enhances the quality and accuracy of our cast components.
Rigorous Quality Control
Our quality control processes encompass advanced inspection techniques like X-ray radiography, ultrasonic testing, and magnetic particle inspection. This comprehensive approach enables us to detect and address any potential defects, ensuring our castings meet the highest industry standards for safety and durability.
Custom Solutions for Automotive Clients
We work closely with our automotive clients to understand their unique requirements and deliver tailored casting and machining solutions. Our team’s expertise enables us to develop components that meet specific design, performance, and durability standards, making Shilpan Steelcast a valuable partner for automotive manufacturers.
Conclusion
Investment casting has become a cornerstone of innovation in the automotive industry, enabling manufacturers to produce high-quality, complex parts that contribute to vehicle efficiency, safety, and performance. At Shilpan Steelcast, our expertise in investment casting, coupled with advanced facilities and stringent quality control, allows us to deliver automotive components that meet the highest standards. As the industry continues to evolve, investment casting will remain a critical process for driving automotive advancements and achieving excellence in manufacturing.
Looking to enhance your automotive components with precision and reliability? Discover how Shilpan Steelcast’s investment casting expertise can meet your needs. Contact us today to learn more about our capabilities and how we can support your next automotive project.