Industry Trends: The Future of Metal Manufacturing and Investment Casting
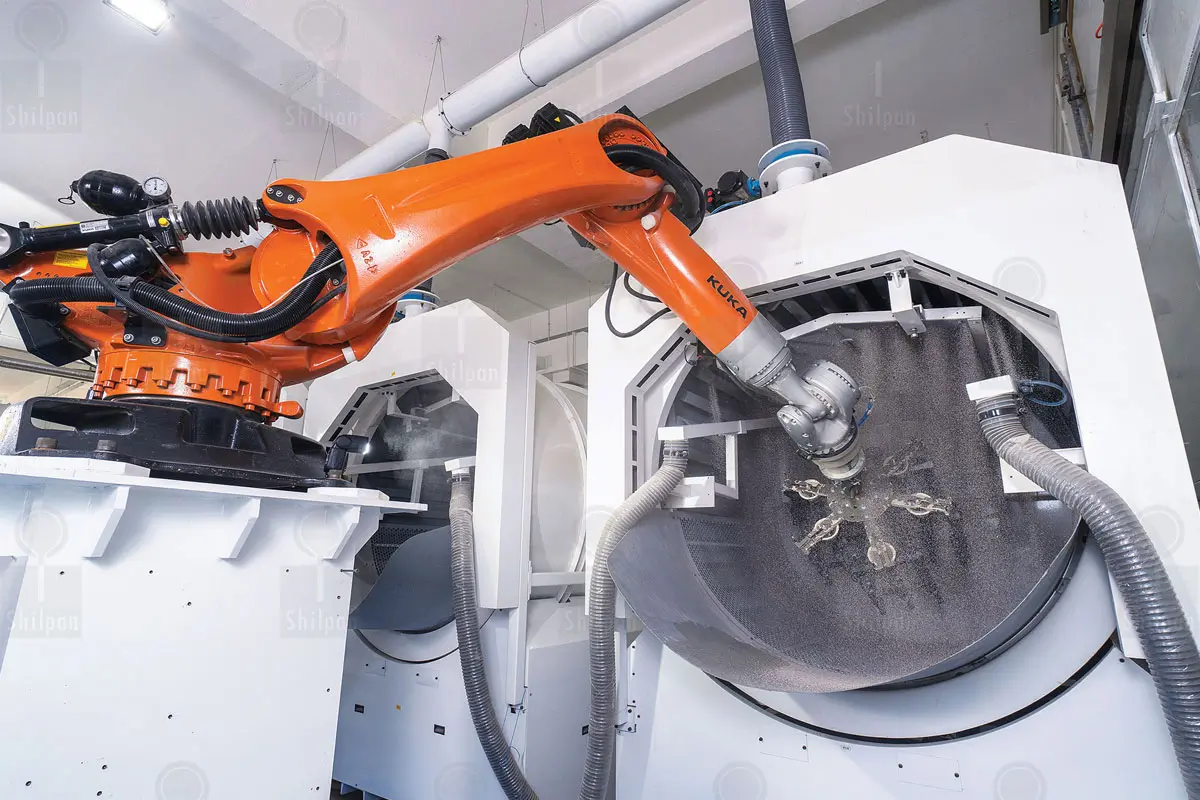
The metal manufacturing industry is at a pivotal moment in its evolution, driven by advancements in technology, increasing demand for sustainability, and the need for precision in modern engineering. Among the many manufacturing processes, investment casting continues to stand out as a reliable, adaptable, and forward-thinking technique. As we look toward the future, it’s essential to understand the key trends shaping the metal manufacturing landscape and how investment casting is adapting to meet the needs of modern industries.
Current Landscape of Metal Manufacturing
Metal manufacturing is a diverse field encompassing processes such as casting, forging, machining, stamping, and additive manufacturing. Recent advancements are pushing the industry toward:
- Lightweight Materials: A surge in demand for alloys like aluminum and titanium is driven by industries seeking to reduce component weight while maintaining durability.
- Precision Engineering: Aerospace, automotive, and healthcare sectors are leading the charge in requiring components with exceptionally tight tolerances and superior quality.
- Automation and Digitalization: Robotics, IoT, and AI are revolutionizing production lines, offering increased efficiency, consistency, and real-time monitoring.
- Sustainability: Reducing waste, energy consumption, and carbon footprints is now a top priority for manufacturers globally.
These trends highlight the industry’s ongoing shift toward more efficient, eco-friendly, and technologically advanced production methods.
Investment Casting: A Timeless Metal Manufacturing Solution
Investment casting, or lost-wax casting, has stood the test of time as one of the most reliable manufacturing processes. Its ability to produce complex, high-precision components with superior surface finishes makes it indispensable across industries such as aerospace, automotive, energy, and healthcare.
Key Advantages of Investment Casting
- High Precision: Produces parts with tight tolerances, reducing the need for additional machining.
- Material Versatility: Suitable for superalloys, stainless steel, titanium, and other specialized materials.
- Cost-Effectiveness: Ideal for complex geometries that would otherwise be expensive to machine.
- Minimal Waste: Wax and material recycling reduce environmental impact.
As industries evolve, investment casting continues to adapt, leveraging new technologies and materials to meet modern demands.
Trends Shaping the Future of Investment Casting
Adoption of Advanced Materials
Industries today require materials with enhanced properties such as corrosion resistance, high strength, and lightweight characteristics. Investment casting has risen to the challenge by accommodating advanced materials, including:
- Superalloys for aerospace and energy sectors due to their heat resistance and durability.
- Titanium Alloys for lightweight, high-strength applications in aerospace and medical fields.
- Aluminum Alloys for automotive components that balance weight reduction with performance.
Automation and Smart Manufacturing
Investment casting is embracing automation and smart technologies to improve efficiency and quality. Key innovations include:
- Robotic Shell Making: Ensures consistent mold production and reduces human error.
- IoT Monitoring: Tracks real-time parameters such as temperature and pressure for optimized casting processes.
- AI-Driven Quality Control: Detects defects and optimizes workflows, reducing waste and improving output.
Sustainability and Eco-Friendly Practices
Environmental concerns are reshaping the industry, and investment casting is no exception. Steps being taken include:
- Energy Efficiency: Modern foundries are using energy-efficient furnaces and adopting renewable energy sources.
- Waste Reduction: Wax recycling and precise mold designs minimize material wastage.
- Eco-Friendly Alloys: Increased use of recyclable and sustainable materials.
Integration with Additive Manufacturing
Additive manufacturing, commonly known as 3D printing, is increasingly complementing investment casting processes. By combining these techniques, manufacturers can:
- Create intricate patterns and prototypes faster.
- Shorten design-to-production cycles.
- Reduce tooling costs.
This hybrid approach is unlocking new possibilities for intricate designs and rapid product development.
Emerging Applications of Investment Casting
The adaptability of investment casting has opened new doors for its applications in various industries:
- Aerospace: Production of turbine blades and other high-performance components.
- Automotive: Lightweight engine components and structural parts.
- Medical Devices: Implants and surgical instruments with high precision.
- Energy: Components for wind turbines, nuclear reactors, and more.
Global Market Demand for Investment Casting
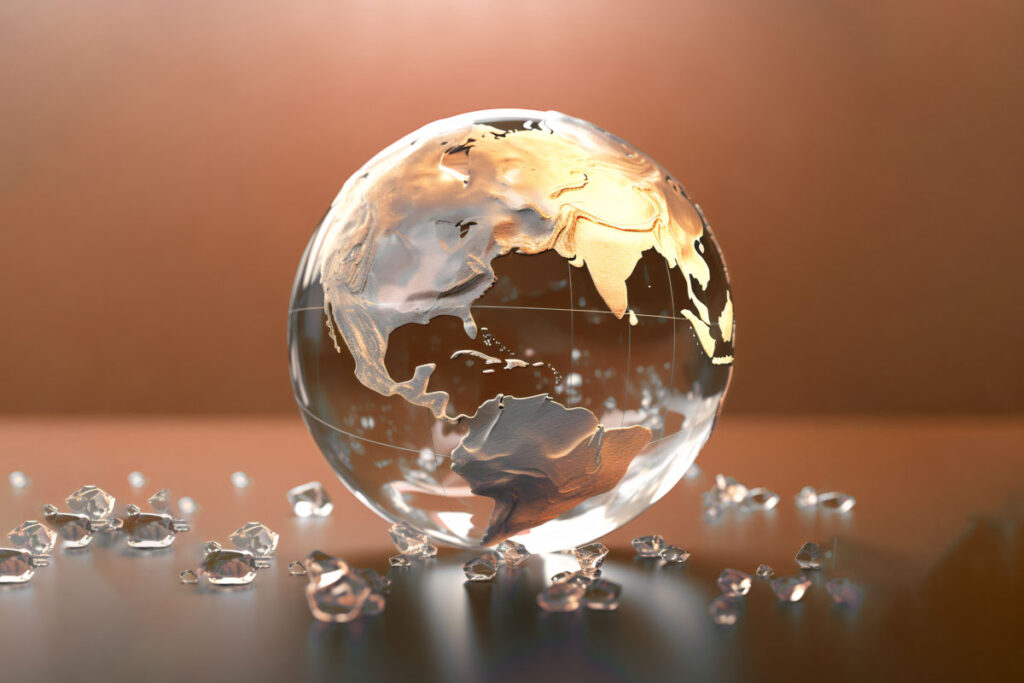
Market Overview
The global investment casting market was valued at USD 16.6 billion in 2022 and is projected to grow at a CAGR of 5.2% from 2023 to 2030. This growth is fueled by increasing demand in sectors like aerospace, automotive, and healthcare.
Regional Insights
- North America: Leads the market with significant demand in aerospace and defense.
- Europe: Growth driven by advanced manufacturing in Germany and green initiatives in the UK.
- Asia-Pacific: Emerging as the fastest-growing region, with China and India spearheading industrial expansion.
Industry Applications
- Aerospace: 35% of the market share.
- Automotive: 25%, driven by lightweight trends.
- Medical Devices: 15%, with high precision demands.
How Shilpan Steelcast is Leading the Way
At Shilpan Steelcast, we embrace industry trends to deliver exceptional solutions. Our capabilities include:
- Advanced Foundry Automation: Robotic systems for shell-making and casting processes.
- Precision Machining Facilities: In-house capabilities for post-casting processes, ensuring complete manufacturing solutions.
- Material Expertise: Working with cutting-edge alloys like superalloys, titanium, and aluminum.
- Global Standards Compliance: Certifications like ISO 9001:2015, IATF 16949:2016, and PED compliance underscore our commitment to quality.
By blending traditional investment casting with modern technologies, we provide components that meet the evolving needs of today’s industries.
Conclusion
Investment casting continues to evolve as a reliable and versatile manufacturing technique, meeting the demands of precision, sustainability, and innovation. As the metal manufacturing industry embraces modern trends, investment casting remains a vital process for producing high-quality components across diverse applications.
At Shilpan Steelcast, we are proud to be at the forefront of these advancements, offering cutting-edge solutions that combine tradition with technology. Whether you need precision-engineered components for aerospace, automotive, or any other industry, our expertise ensures exceptional results.
Contact us today to learn how we can support your manufacturing needs with precision and reliability.