How Material Selection Impacts the Quality and Performance of Investment Casting Products
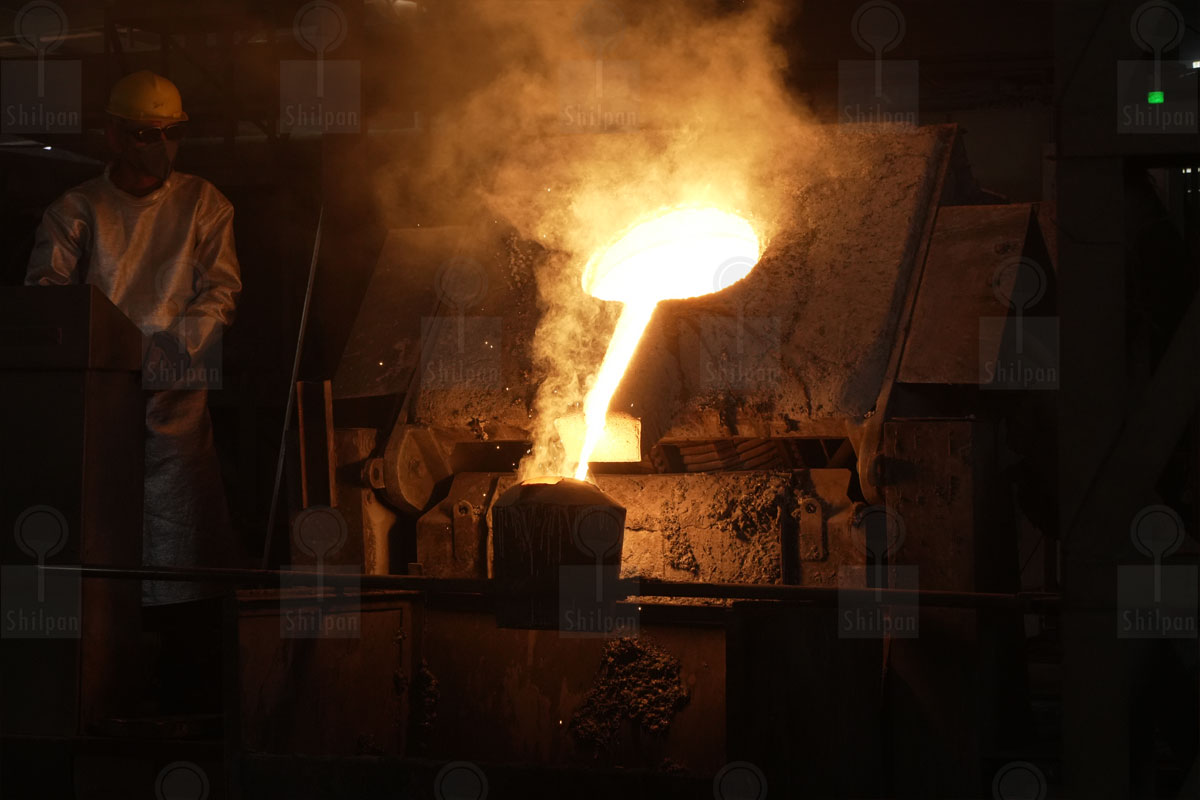
When it comes to investment casting, material selection is more than a technical step—it is the foundation of a product’s performance, durability, and cost-efficiency. The right alloy ensures a casting will endure its intended environment, resist wear or corrosion, and meet dimensional precision even under stress. The wrong choice can result in premature failure, costly redesigns, or compromised safety.
At Shilpan Steelcast, one of the top investment casting manufacturers in India, material selection is a critical part of both design and production. With a world-class investment casting foundry in Rajkot, India, the company leverages decades of metallurgical expertise to guide customers in choosing the ideal materials for every application—from automotive parts to oil & gas equipment and beyond.
Why Material Matters in Investment Casting
Unlike many other metal manufacturing methods, investment casting allows the use of a vast range of materials, including stainless steels, carbon steels, tool steels, nickel alloys, cobalt alloys, and even precious metals. This versatility enables Shilpan Steelcast to cater to multiple industries with varied performance needs.
Material properties directly affect:
- Mechanical strength (tensile, yield, impact resistance)
- Corrosion and oxidation resistance
- Wear and abrasion characteristics
- Thermal conductivity and resistance
- Machinability and post-processing potential
- Component weight and density
For industries such as aerospace, automotive, railways, and energy, where failure is not an option, choosing the right material means securing long-term reliability and safety.
Factors That Influence Material Selection in Investment Casting
1. Intended Application and Service Conditions
Is the part exposed to high temperatures? Does it need to withstand corrosive fluids or abrasive environments? The answers determine whether the casting will be made from:
- Stainless Steel (Grades 304, 316, 410, etc.) – For excellent corrosion resistance in food processing, marine, and chemical industries.
- Carbon Steel – For components where strength is essential, such as heavy machinery or railways.
- Nickel or Cobalt-Based Alloys – For extreme environments like oil & gas, aerospace, or energy sectors.
- Tool Steels – When wear resistance and toughness are critical.
At Shilpan Steelcast, engineers collaborate closely with customers to match material properties with real-world application needs, ensuring optimal performance and lifespan.
2. Mechanical and Dimensional Requirements
Some investment cast parts require high tensile strength and toughness, while others need tight dimensional tolerances for precise assembly. Material behavior during the investment casting process—including shrinkage, fluidity, and solidification patterns—affects dimensional control.
Shilpan’s advanced simulation software and DFM (Design for Manufacturability) services predict these factors, helping to fine-tune material selection for minimal distortion and machining ease.
3. Corrosion and Wear Resistance Demands
For industries like marine, chemical processing, and oil & gas, corrosion resistance is critical. Materials like:
- Duplex Stainless Steels (combining strength and corrosion resistance),
- Hastelloy,
- Inconel, or
- Superalloys
are often selected to withstand harsh chemicals, saltwater, or high-pressure steam.
Shilpan Steelcast ensures such choices align not only with environmental demands but also with international quality standards like PED 2014/68/EU, AD 2000-Merkblatt W0, and IATF 16949:2016, ensuring castings meet both performance and certification expectations.
4. Machinability and Post-Processing Considerations
Material choice also impacts precision machining—a key value-added service at Shilpan’s Rajkot facility. Alloys that are difficult to machine may require adjustments in casting design to reduce post-processing time and costs.
Through its in-house CNC machining and surface treatment services, Shilpan ensures that the selected material delivers not just in function but also in manufacturability, keeping costs under control without compromising quality.
5. Cost vs. Performance Balance
Premium alloys offer unmatched performance but come at a cost. Shilpan’s engineering team helps customers balance material performance with project budgets—sometimes recommending cost-effective alternatives that meet essential performance criteria without inflating expenses.
This consultative approach ensures long-term customer satisfaction and competitive product pricing.
Commonly Used Materials in Shilpan Steelcast’s Investment Casting Foundry
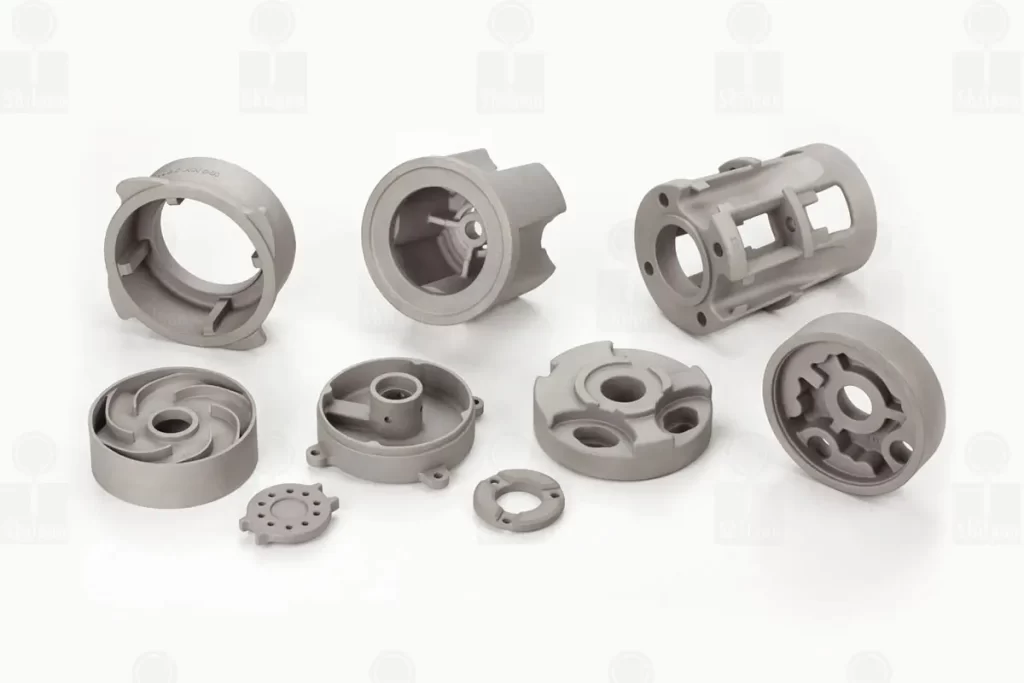
As one of India’s most trusted investment casting manufacturers, Shilpan Steelcast offers a broad portfolio of materials, including:
Material Type | Typical Applications |
---|---|
Stainless Steels | Pump parts, valves, food processing, marine |
Carbon & Alloy Steels | Automotive parts, general engineering |
Duplex Steels | Oil & gas, chemical processing |
Tool Steels | Wear parts, cutting tools |
Nickel Alloys | Aerospace, energy, chemical environments |
Cobalt Alloys | Medical implants, high-temperature parts |
Each material batch is tested in Shilpan’s world-class Quality Lab, using spectrometers, CMMs, tensile testers, and impact testers, ensuring chemical composition and mechanical integrity meet exacting global standards.
Case Example: Material Selection in Action
An American automotive manufacturer approached Shilpan Steelcast for the development of suspension system components designed for light commercial vehicles. The challenge was to identify a material that could endure cyclic loading, provide excellent fatigue resistance, and withstand corrosive road conditions such as exposure to de-icing salts common in North America.
After a detailed analysis of the component’s load profile, environmental exposure, and manufacturability considerations, Shilpan’s engineering team recommended a high-strength low-alloy (HSLA) steel. This choice offered an ideal balance of:
- Superior fatigue strength for extended service life under variable loads.
- Improved corrosion resistance compared to standard carbon steels, reducing rust formation.
- Cost efficiency, meeting the customer’s budget constraints while avoiding over-engineering.
Incorporating this material allowed the customer to achieve:
- Longer part durability, minimizing field failures.
- Reduced maintenance frequency and costs for fleet operators.
- Weight optimization to improve vehicle fuel efficiency—an important consideration for regulatory compliance in the U.S. automotive market.
This tailored material selection not only met the mechanical and environmental demands but also aligned with IATF 16949:2016 automotive quality management standards, ensuring the castings seamlessly integrated into the client’s certified production systems.
Such engineering consultation reflects Shilpan Steelcast’s commitment to adding value beyond casting by being a trusted material and process advisor to global customers.
Material Selection—The Cornerstone of Investment Casting Success
Material choice is not an afterthought in investment casting—it shapes every aspect of a product’s life cycle, from casting performance to field reliability. At Shilpan Steelcast, this process is guided by metallurgical expertise, global quality certifications, and a customer-first mindset.
As a globally trusted investment casting foundry in Rajkot, India, serving industries from automotive to oil & gas, Shilpan Steelcast stands as a partner committed to material excellence, ensuring every casting delivers lasting value, performance, and safety.
For customers worldwide, this focus on material integrity is what makes Shilpan Steelcast a leader in precision machining, casting quality, and export reliability.
Ready to Elevate Your Investment Cast Products with the Right Material?
Partner with Shilpan Steelcast and benefit from expert metallurgical guidance, world-class production capabilities, and certified quality assurance. Whether you need high-performance alloys or cost-effective solutions, our team is here to help you make the smartest material choices for your applications.
Contact us today to discuss your next project or request a customized consultation.