Common Defects in Investment Casting and How to Prevent Them
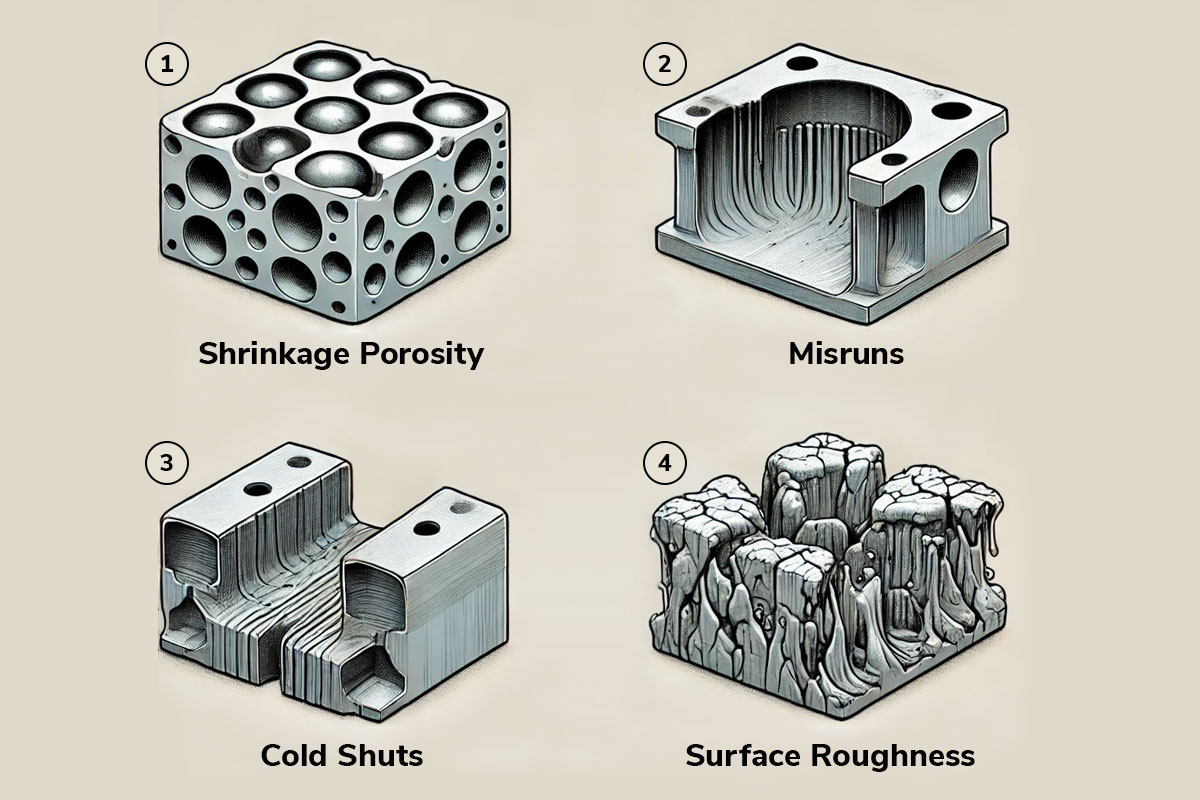
Investment casting or lost-wax casting is renowned for its high precision, intricate designs, and superior surface finish, making it one of the most preferred manufacturing methods for metal components across industries. However, like any manufacturing process, investment casting is not immune to defects. Understanding common investment casting defects and how to prevent them is crucial to achieving consistent quality and reliability.
In this article, we’ll explore the most frequent defects in investment casting, their causes, and how manufacturers like Shilpan Steelcast implement advanced techniques to minimize these issues — delivering defect-free precision metal components.
Why Defect Prevention Matters in Investment Casting
Defects in investment casting can significantly impact the performance, aesthetics, and lifespan of components. Particularly in industries like automotive, aerospace, medical, and energy, where precision and durability are critical, even the slightest defect can lead to product failure or rejection.
By identifying common defects and applying rigorous quality control practices, manufacturers can produce high-quality castings that meet exact specifications.
Common Investment Casting Defects and Their Prevention
Investment casting defects can occur at different stages of the manufacturing process — from pattern making to final finishing. Below are some of the most frequent defects, their causes, and the methods to prevent them:
1. Porosity
Porosity refers to small voids or air bubbles trapped inside the casting.
Causes:
- Air entrapment during metal pouring
- Poor wax pattern quality
- Incorrect gating system design
- Inadequate de-gassing of molten metal
Prevention:
- Proper venting systems in the mould
- Degassing of molten metal before pouring
- High-quality wax patterns with uniform thickness
- Optimized gating and sprue designs
2. Shrinkage Cavities
Shrinkage cavities are internal or external voids that form when metal contracts as it cools.
Causes:
- Insufficient metal supply during solidification
- Poor gating system design
- Incorrect pouring temperature
Prevention:
- Use of feeder heads and risers to supply additional molten metal
- Optimized mould design to promote uniform solidification
- Controlled pouring temperatures
3. Misruns
Misruns occur when the molten metal solidifies before completely filling the mould cavity.
Causes:
- Low pouring temperature
- Slow metal flow rate
- Poor mould preheating
Prevention:
- Proper preheating of ceramic shells
- Maintaining optimal metal pouring temperature
- Improved gating system design
4. Surface Cracks
Surface cracks are visible cracks on the surface of the casting, compromising structural integrity.
Causes:
- Thermal stress during solidification
- Rapid cooling
- Low mould strength
Prevention:
- Gradual cooling processes
- High-quality ceramic shells
- Stress-relieving heat treatment
5. Inclusions
Inclusions are foreign materials or impurities embedded in the casting surface.
Causes:
- Poor metal filtration
- Contaminated molten metal
- Damaged mould shells
Prevention:
- Use of ceramic filters during metal pouring
- Regular inspection and cleaning of molten metal
- High-quality ceramic shell preparation
6. Gas Holes
Gas holes are small cavities formed by trapped gases during solidification.
Causes:
- Moisture in mould shells
- Poor de-gassing of molten metal
- Rapid pouring speed
Prevention:
- Preheating mould shells to remove moisture
- Proper molten metal degassing
- Controlled pouring speed
7. Dimensional Inaccuracy
Dimensional inaccuracies can result in parts that don’t meet specified tolerances.
Causes:
- Wax pattern shrinkage
- Mould deformation
- Inconsistent casting process parameters
Prevention:
- Precision wax pattern injection systems
- Rigorous mould inspection
- Advanced CNC machining for post-casting finishing
8. Hot Tears
Hot tears are cracks that form during solidification due to thermal stress when the metal cannot shrink freely.
Causes:
- Poor mould design
- High cooling rates
- Rigid ceramic shell materials
Prevention:
- Using flexible ceramic shells that allow for metal shrinkage
- Controlled cooling rates
- Proper mould design with smooth transitions and fillets
9. Wax Pattern Defects
Defects in wax patterns like cracks, bubbles, or deformations can directly transfer to the final casting.
Causes:
- Improper wax injection temperature
- Poor quality wax
- Handling errors
Prevention:
- Use of high-quality wax materials
- Optimized wax injection parameters
- Strict inspection of wax patterns before moulding
10. Metal Penetration
Metal penetration happens when molten metal infiltrates into the ceramic mould, causing rough surface finishes.
Causes:
- Low ceramic shell density
- High pouring temperature
- Poor surface coating of the mould
Prevention:
- Improved ceramic shell quality
- Proper mould coating thickness
- Controlled metal pouring temperatures
How Shilpan Steelcast Ensures Defect-Free Investment Castings
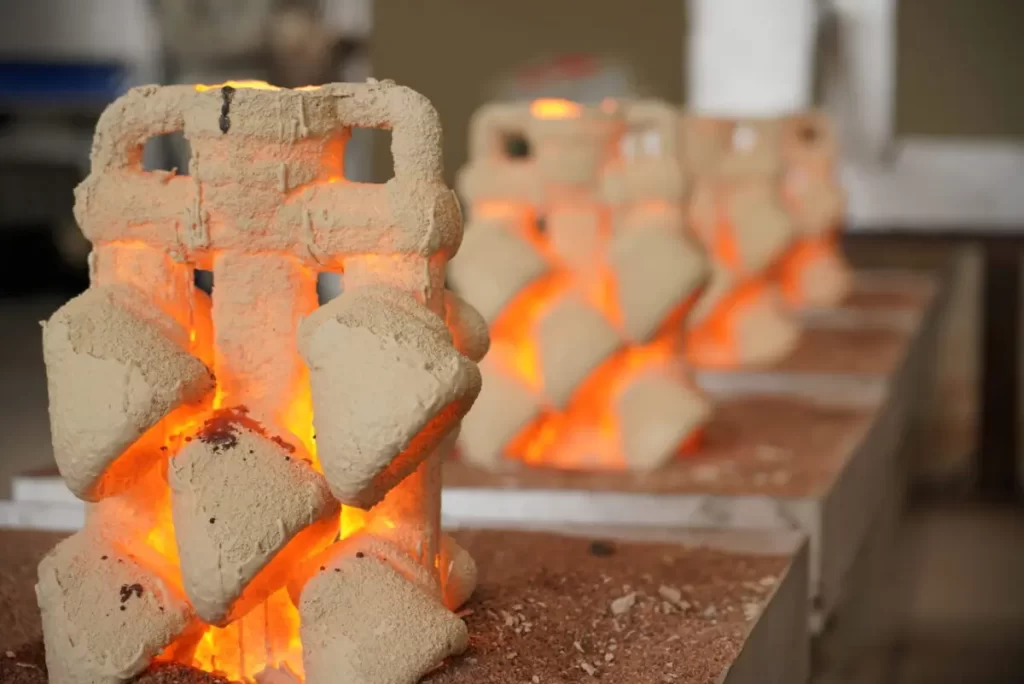
At Shilpan Steelcast, we understand that quality is non-negotiable when it comes to precision metal components. Our comprehensive quality control system ensures that every casting meets the highest industry standards.
Here’s how we minimize casting defects:
- Advanced Wax Injection Machines for consistent pattern quality
- In-house Non-Destructive Testing (NDT) methods like X-ray inspection, ultrasonic testing, and magnetic particle inspection
- Automated Shell-Building Systems for consistent ceramic mould production
- High-end Induction Furnaces with metal degassing systems
- Precision Heat Treatment Facilities to improve mechanical properties and stress relief
- Strict final inspection with CMM (Coordinate Measuring Machines)
Conclusion
Defect prevention is a critical aspect of investment casting, ensuring the production of high-quality, precision-engineered components across industries. By understanding the common defects and implementing advanced quality control measures, manufacturers can enhance product performance, reduce waste, and improve customer satisfaction.
At Shilpan Steelcast, our commitment to quality, innovation, and sustainability sets us apart as one of the leading investment casting manufacturers in India. With advanced technologies, state-of-the-art manufacturing facilities, and skilled craftsmanship, we deliver castings that meet the highest standards of precision and reliability.
Whether you need high-performance components for aerospace, automotive parts, or custom-engineered castings, Shilpan Steelcast is your trusted partner in precision metal manufacturing.
Contact Us
Get in touch with us to learn more about our investment casting capabilities and how we can support your next project with defect-free precision components.