What is Rolled Ring Forging? Process, Benefits, and Industry Applications
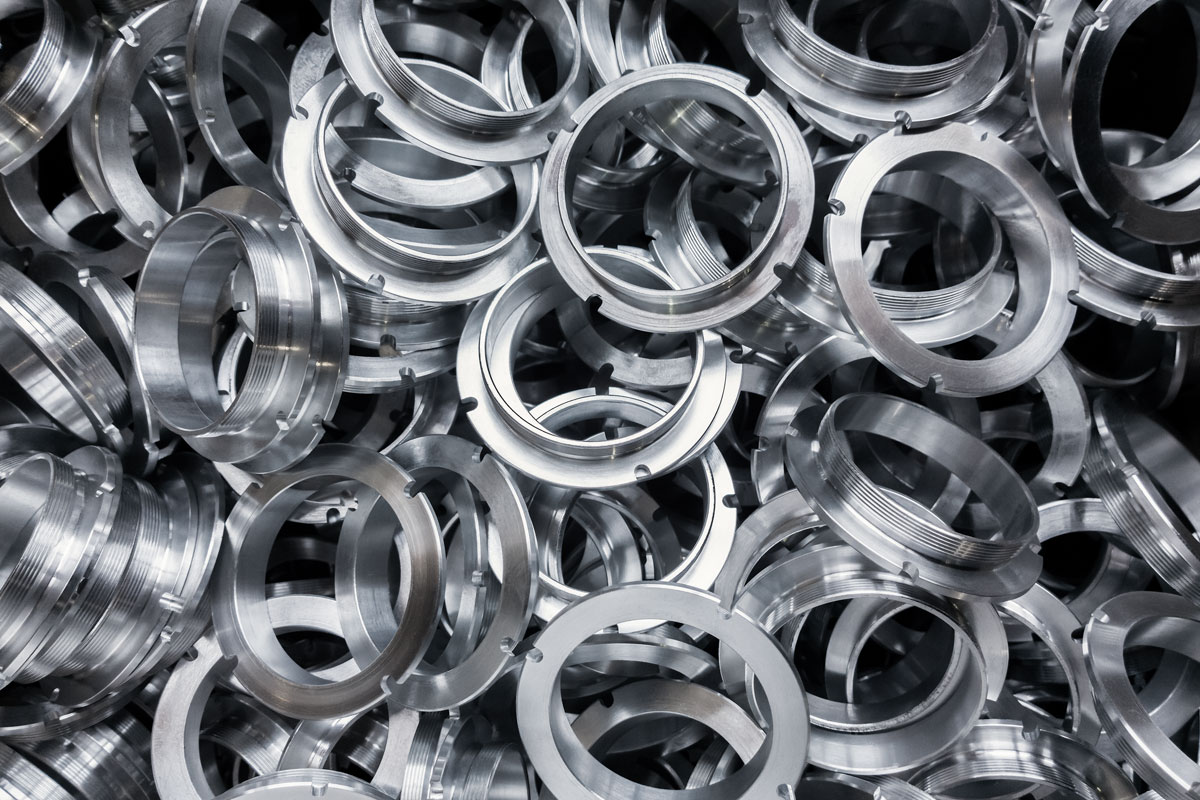
In the realm of metal forging, Rolled Ring Forging is a highly specialized and efficient manufacturing process that produces seamless, high-strength metal rings. These rings are essential components in industries where performance, reliability, and durability are non-negotiable. Unlike other ring manufacturing methods, rolled ring forging offers superior grain flow, enhanced mechanical properties, and the ability to create large-diameter rings with varying cross-sections. This makes it a preferred technique for critical applications across diverse industries, including manufacturing ring flanges, a specialty of Shilpan Steelcast.
At Shilpan Steelcast, we specialize in manufacturing precision-engineered ring flanges using rolled ring forging, ensuring durability and precision for critical applications. Our advanced forging capabilities allow us to deliver superior-quality forged components that meet stringent industry standards.
What is Rolled Ring Forging?
Rolled ring forging is a metal forming process that transforms a preformed metal billet into a seamless ring through a combination of heat, pressure, and rotational force. The process begins with a cylindrical billet, which is heated to a specific temperature to enhance its malleability. The billet is then pierced to create a hollow preform, often referred to as a “donut.” This preform is placed on a mandrel and subjected to radial rolling, which expands the ring to the desired diameter and thickness while refining its grain structure.
The result is a seamless ring with a continuous grain flow that follows the contour of the ring. This unique grain structure enhances the mechanical properties of the ring, making it stronger, more durable, and resistant to fatigue and stress fractures. Unlike welded rings, rolled ring forgings have no weak points, ensuring superior structural integrity.
Understanding the Rolled Ring Forging Process
The rolled ring forging process is a carefully controlled sequence of operations that transforms a heated metal billet into a high-quality, seamless ring. Here’s a breakdown of the key stages:
- Billet Preparation: The process begins with a precisely sized billet of the chosen metal alloy. This billet is then heated to a forging temperature, which varies depending on the material. Careful temperature control is crucial to ensure optimal plasticity and prevent defects.
- Piercing: The heated billet is then pierced, creating a hollow cylindrical preform. This piercing operation is typically done using a hydraulic press and a mandrel.
- Ring Rolling: The pierced preform is placed onto a mandrel, which acts as an internal support. The mandrel, along with the preform, rotates while being subjected to compressive forces from external rolls. These rolls progressively reduce the wall thickness and increase the diameter of the ring. This controlled deformation refines the grain structure of the metal, resulting in improved strength, toughness, and fatigue resistance.
- Sizing and Shaping: The ring rolling process continues until the desired diameter and shape are achieved. Different roll profiles can be used to create rings with varying cross-sections, including rectangular, circular, or custom shapes.
- Cutting and Separation: Once the ring has reached its final dimensions, it is cut from the remaining material.
- Cooling: The forged ring is then cooled in a controlled environment. The cooling rate can significantly influence the final properties of the ring.
- Finishing Operations (Optional): Depending on the application, the forged ring may undergo further processing, such as heat treatment (annealing, normalizing, quenching, tempering), machining, or surface finishing. These operations are performed to achieve final dimensions, desired mechanical properties, and surface quality.
Materials Used in Rolled Ring Forging
Various metals and alloys can be used in rolled ring forging to meet industry-specific requirements:
- Carbon Steel – Cost-effective and strong, commonly used in general engineering applications.
- Alloy Steel – Enhanced strength and wear resistance, ideal for heavy-duty applications.
- Stainless Steel – Corrosion-resistant and durable, widely used in aerospace and medical industries.
- Aluminum – Lightweight and suitable for aerospace and automotive applications.
- Titanium – High strength-to-weight ratio, ideal for critical components in high-performance industries.
Key Benefits of Rolled Ring Forging
Rolled ring forging offers numerous advantages over traditional manufacturing methods:
- Superior Strength and Durability: The deformation process refines the metal’s grain structure, eliminating internal voids and creating a continuous grain flow. This leads to enhanced mechanical properties, including tensile strength, yield strength, impact resistance, and fatigue strength.
- Seamless Construction: Rolled rings are seamless, eliminating the weaknesses associated with welded or joined rings. This makes them ideal for high-stress applications where structural integrity is paramount.
- Precise Dimensions and Tolerances: The controlled rolling process allows for precise control over ring dimensions and tolerances, minimizing the need for costly and time-consuming machining.
- Versatility in Size and Shape: Rolled ring forging can produce rings of various diameters, from small bearing races to large diameter flanges. It can also create rings with varying cross-sections, catering to diverse application requirements.
- Cost-Effectiveness for Large Production Runs: While initial tooling costs may be higher, the efficiency and high material utilization of the process make it cost-effective for large-scale production.
- Improved Material Utilization: The process minimizes material waste compared to other manufacturing methods, contributing to cost savings and environmental sustainability.
Industry Applications
Rolled ring forgings are widely used in various industries due to their exceptional performance characteristics:
- Automotive: Wheel rims, gears, bearing races, transmission components
- Aerospace: Landing gear components, engine parts, turbine rings, structural components
- Wind Energy: Gear rings, bearing rings, tower flanges, yaw and pitch bearings
- Oil and Gas: Pipeline flanges, valve components, drill collars, subsea equipment
- Heavy Machinery: Sprockets, gears, bearing supports, slewing rings
- Off-Highway Equipment: Track rollers, swing gears, axle components
- Ring Flanges: Connecting pipes, valves, and other equipment in various industrial applications (a key product of Shilpan Steelcast
Why Choose Rolled Ring Forging Over Other Methods?
Compared to other manufacturing techniques, rolled ring forging offers distinct advantages:
- Stronger than Casting – Rolled ring forging refines grain structure, while casting can have internal porosity.
- More Cost-Effective than Machining – Produces near-net shape parts, reducing material waste.
- Better than Open-Die Forging – Provides greater consistency and precision for ring-shaped components.
- Ideal for Custom Applications – Rings can be produced in various sizes, materials, and thicknesses.
Shilpan Steelcast’s Expertise

At Shilpan Steelcast, we specialize in precision ring flanges using rolled ring forging, ensuring strength, dimensional accuracy, and superior performance. Our advanced forging capabilities include:
- Advanced Technology: We utilize the latest forging and rolling equipment to ensure precision and consistency in every product.
- In-House Precision Machining: Our advanced precision machining facilities allow us to produce ring flanges with tight tolerances and superior surface finish.
- Material Expertise: Our team has extensive knowledge of various metals and alloys, allowing us to recommend the best material for your application.
- Quality Assurance: Every rolled ring undergoes rigorous testing and inspection to ensure it meets the highest standards of quality and performance.
- Custom Solutions: We work closely with our clients to develop customized solutions that address their unique challenges and requirements.
- Global Reach: With a strong presence in international markets, we are a trusted partner for industries worldwide.
Conclusion
Rolled ring forging remains one of the most reliable metal-forming techniques, offering exceptional strength, cost efficiency, and design flexibility. As industries demand high-performance components, the process continues to evolve to meet modern engineering challenges.
At Shilpan Steelcast, we take pride in being a trusted partner for industries that demand the highest standards of performance and reliability. Our expertise, advanced technology, and commitment to quality ensure that every rolled ring we produce—including our specialized Ring Flanges—is built to last.
Looking for precision-engineered rolled ring forgings?
Contact Shilpan Steelcast today to discuss your rolled ring forging and ring flange needs, and discover how we can provide solutions that meet your specific requirements.