Metal Forging: Techniques, Benefits, and Applications
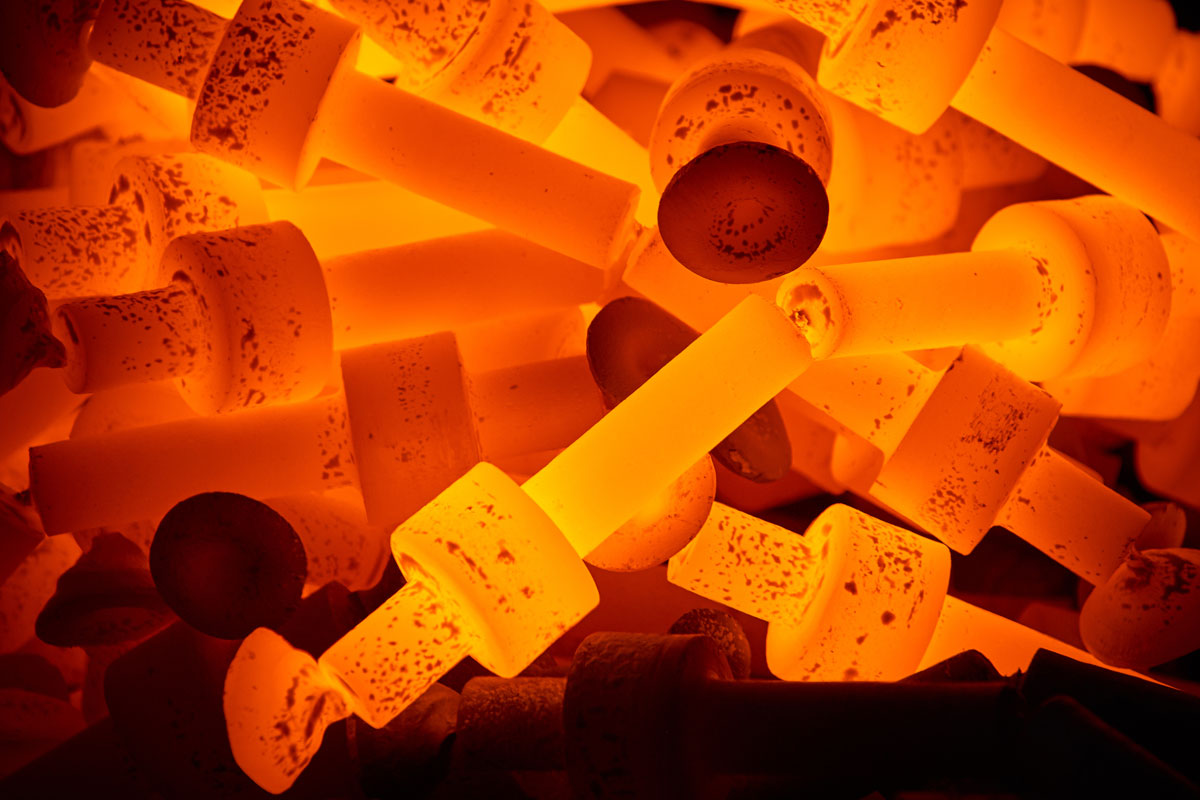
In the realm of metalworking, forging stands as an ancient art that continues to shape the modern world. From intricate components to robust structures, forging plays a vital role in crafting metal with precision and strength. In this comprehensive guide, we’ll explore the diverse techniques and applications of forging, shedding light on its significance in today’s manufacturing landscape.
Forging is a time-honored craft that has been practiced for centuries, dating back to ancient civilizations. It involves shaping metal into desired forms through the application of heat and pressure. The process not only enhances the mechanical properties of the metal but also refines its grain structure, resulting in superior strength, toughness, and durability.
Traditionally, forging was carried out by skilled blacksmiths using hammers and anvils. However, modern forging techniques have evolved significantly, incorporating advanced machinery and automation to achieve higher precision and efficiency.
What is Metal Forging?
At its core, forging is a manufacturing process that involves shaping metal using compressive forces. This process is carried out at elevated temperatures, known as hot forging, or at room temperature, known as cold forging. In hot forging, the metal is heated to temperatures above its recrystallization point to improve its formability and reduce the force required for deformation. Commonly forged metals include steel, aluminium, titanium, and copper alloys. Each metal exhibits unique characteristics that make it suitable for specific applications, ranging from automotive components to aerospace parts. By applying pressure, heat, or both, raw materials are transformed into desired shapes with enhanced mechanical properties.
What are the Different Types of Forgings?
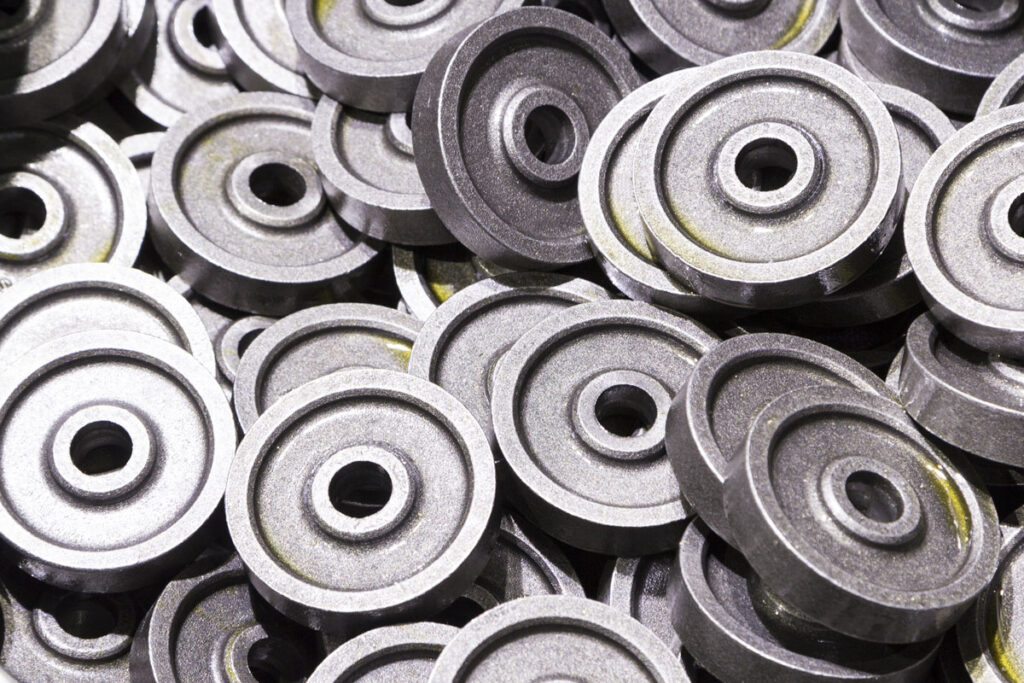
The forging process can be broadly categorized into three main techniques:
Open Die Forging: Also known as free forging, open die forging involves deforming a piece of metal between multiple dies that do not completely enclose the material. This technique allows for greater flexibility in shaping large and complex parts while maintaining material integrity.
Closed Die Forging: In closed die forging, the metal is placed within a set of dies that contain a cavity of the desired shape. As the dies close, the metal is compressed to fill the mould, resulting in precise and intricate components with minimal waste.
Press Forging: Press forging utilizes hydraulic or mechanical presses to apply controlled pressure to the metal, forcing it into a die cavity. This method offers versatility in shaping both simple and complex parts, with the ability to achieve tight tolerances and uniformity.
Hot Forging vs. Cold Forging
Hot Forging: Hot forging involves heating the metal above its recrystallization temperature, making it more malleable and easier to deform. This method is ideal for shaping materials such as steel, aluminium, and titanium, allowing for greater formability and reduced risk of work hardening.
Cold Forging: Cold forging, on the other hand, occurs at or near room temperature, preserving the material’s grain structure and enhancing its strength. While cold forging requires greater force than hot forging, it offers advantages such as improved dimensional accuracy, surface finish, and material savings.
Benefits and Applications of Forging: Strength in Precision
Metals Used in Forging
Forging can be performed on a wide range of metals and alloys, each offering unique properties and advantages. Some of the most commonly forged metals include:
Steel: Known for its strength, durability, and versatility, steel is one of the most widely used metals in forging. It can be forged into various shapes and sizes, making it suitable for a wide range of applications, including automotive, construction, and manufacturing.
Aluminium: Lightweight and corrosion-resistant, aluminium is ideal for applications where weight reduction is critical, such as aerospace and automotive industries. It can be forged into complex shapes with high precision, offering an excellent strength-to-weight ratio.
Titanium: Renowned for its exceptional strength-to-weight ratio and corrosion resistance, titanium is commonly used in high-performance applications, such as aerospace components, medical implants, and sporting goods.
Copper Alloys: Copper alloys, such as bronze and brass, are valued for their excellent conductivity, corrosion resistance, and aesthetic appeal. They are commonly forged into intricate shapes for use in electrical and plumbing applications, decorative art, and musical instruments.
By understanding the properties and characteristics of different metals, manufacturers can select the most suitable material for their forging applications, ensuring optimal performance and durability of the finished components.
Benefits and Applications of Forging
Forging offers a multitude of benefits that make it indispensable in various industries:
Enhanced Strength: The controlled deformation of metal during forging results in improved grain structure and mechanical properties, including higher strength, toughness, and fatigue resistance.
Precision Engineering: With the ability to achieve tight tolerances and intricate shapes, forging delivers components with exceptional dimensional accuracy and surface finish.
Cost Efficiency: By minimizing material waste and secondary machining operations, forging reduces production costs while maximizing material utilization.
Versatile Applications: From automotive and aerospace to energy and construction, forging finds applications in a wide range of industries, producing components for engines, turbines, gears, shafts, and more.
Forging Ahead: Partnering with Shilpan Steelcast
At Shilpan Steelcast, we leverage decades of expertise to deliver precision forged components that exceed industry standards. Our comprehensive forging capabilities encompass open die forging, closed die forging, and press forging, allowing us to meet the diverse needs of our clients across industries. Whether you require high-strength components for aerospace engines or intricate parts for automotive transmissions, we’re here to forge the future of metalworking with excellence and innovation.
Ready to Explore the World of Forging? Contact us today to discuss your forging requirements and experience the excellence of Shilpan Steelcast.