Drop Forging: Open-die vs. Closed-die – Choosing the Best Forging Process for Your Project
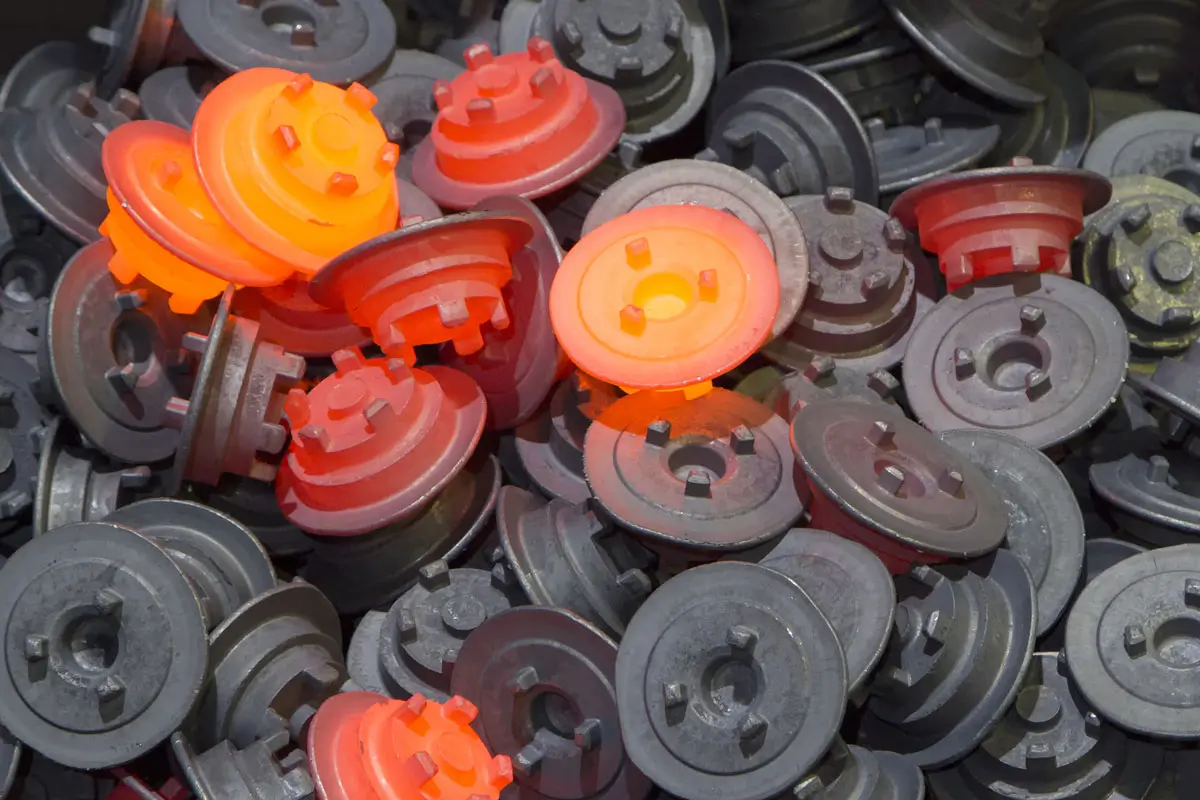
What is Forging?
Forging is one of the most time-tested metalworking techniques, producing strong and reliable components for various industries. Among the different types of forging, drop forging has become an essential process due to its ability to create parts with superior mechanical properties and durability. However, selecting the right drop forging process is critical to achieving optimal results for your project. This article explores the two main types of drop forging—open-die and closed-die—and provides insights into choosing the best option for your specific needs.
What is Drop Forging?
Drop forging is a metal shaping process where a hammer or press is used to apply force to a heated metal piece, shaping it into the desired form. The process involves high-pressure impact, which not only deforms the metal but also improves its grain structure and mechanical strength. Drop forging is widely used in industries such as automotive, aerospace, oil and gas, and heavy machinery manufacturing, where strength and precision are paramount.
Two primary categories of drop forging dominate the industry: open-die forging and closed-die forging. Each has distinct advantages, making them suitable for different applications.
Open-die Drop Forging
Open-die forging, often called free-form forging, involves deforming a heated metal workpiece between two flat or contoured dies that do not enclose the metal completely. The metal is manually manipulated or repositioned to achieve the desired shape.
Advantages of Open-die Forging
- Ideal for Large Components: Open-die forging can produce massive parts, such as large shafts, gears, and flanges, making it suitable for heavy industries like power generation and shipbuilding.
- Excellent Grain Structure: The process refines the metal’s grain flow, enhancing its strength, toughness, and fatigue resistance.
- Flexibility in Shapes and Materials: Open-die forging accommodates a wide range of materials and allows for greater customization of shapes.
Disadvantages of Open-die Forging
- Lower Precision: The process lacks the precision of closed-die forging, making it less suitable for intricate designs or high-tolerance requirements.
- Skilled Operators Required: Open-die forging relies heavily on operator expertise, increasing the margin for human error.
Common Applications
- Large industrial components, such as shafts, rollers, and pressure vessels.
- Custom parts for industries like oil and gas and construction equipment manufacturing.
Closed-die Drop Forging
Closed-die forging, also known as impression die forging, involves shaping heated metal within a set of dies that enclose the material completely. The dies feature pre-designed cavities that determine the final shape of the component.
Advantages of Closed-die Forging
- High Precision and Accuracy: Closed-die forging produces near-net shapes with tight tolerances, reducing the need for extensive machining.
- Minimal Material Waste: The process ensures better material utilization, leading to cost savings in high-volume production.
- Mass Production Capability: Ideal for producing large quantities of identical components with consistent quality.
Disadvantages of Closed-die Forging
- High Initial Tooling Costs: The creation of custom dies can be expensive, making this process more suitable for larger production runs.
- Size Limitations: Closed-die forging is better suited for smaller to medium-sized components.
Common Applications
- Automotive parts, such as gears, connecting rods, and crankshafts.
- Aerospace components requiring high precision and durability.
- Industrial tools and smaller, intricate metal parts.
Key Differences Between Open-die and Closed-die Drop Forging
Factor | Open-die Forging | Closed-die Forging |
---|---|---|
Component Size | Suitable for large parts. | Suitable for small to medium-sized parts. |
Precision | Lower precision; requires post-processing. | High precision with minimal machining. |
Material Utilization | Greater waste; requires more material. | Efficient use of material, minimal waste. |
Tooling Cost | Lower tooling costs. | Higher initial tooling costs. |
Production Volume | Ideal for small batches or custom parts. | Best for mass production of identical parts. |
Choosing between the two processes depends on the specific requirements of your project, such as size, complexity, and budget.
Factors to Consider When Choosing a Drop Forging Process
When deciding between open-die and closed-die forging for your project, consider the following factors:
- Component Size and Shape: Large, simple shapes are better suited for open-die forging, while smaller, complex parts benefit from closed-die forging.
- Precision and Tolerances: If tight tolerances and intricate designs are needed, closed-die forging is the better choice.
- Material Properties: Both processes offer excellent mechanical strength, but the choice may depend on the specific material and grain flow requirements.
- Production Volume: Open-die forging is cost-effective for low-volume, custom parts, while closed-die forging excels in high-volume production.
- Budget: Consider initial tooling costs and overall production expenses.
Materials Used in Drop Forging
Drop forging is a versatile process that can accommodate a wide variety of materials, making it suitable for numerous industries and applications. The choice of material plays a critical role in determining the strength, durability, and performance of the forged component. At Shilpan Steelcast, we specialize in working with high-quality materials to meet the diverse needs of our clients.
Steel (Carbon Steel, Alloy Steel, and Stainless Steel)
Steel is one of the most widely used materials in drop forging due to its exceptional strength, toughness, and resistance to wear and tear. Carbon steel is preferred for its cost-effectiveness, alloy steel for its improved mechanical properties, and stainless steel for its corrosion resistance.
Aluminum
Aluminum is lightweight yet strong, making it an ideal choice for industries like aerospace, automotive, and transportation. Its high corrosion resistance and excellent thermal conductivity are added advantages.
Copper and Copper Alloys (Brass and Bronze)
Copper and its alloys offer high electrical and thermal conductivity, making them suitable for electrical components, fittings, and decorative parts. They also provide good corrosion resistance and machinability.
Titanium
Titanium is highly valued for its excellent strength-to-weight ratio, corrosion resistance, and ability to withstand high temperatures. It is widely used in aerospace, medical, and high-performance automotive applications.
Nickel Alloys
Nickel-based alloys, known for their ability to withstand extreme conditions, are often used in industries like oil and gas, power generation, and chemical processing.
Magnesium
Magnesium is another lightweight material, commonly used in industries where weight reduction is critical, such as aerospace and automotive manufacturing.
Why Material Selection Matters in Drop Forging
The material used in drop forging plays a critical role in determining the properties of the final product. Factors such as mechanical strength, ductility, hardness, and resistance to environmental factors like corrosion and heat should align with the intended application. At Shilpan Steelcast, we help clients select the most suitable materials for their projects, ensuring optimal performance and durability.
How Shilpan Steelcast Can Help with Drop Forging
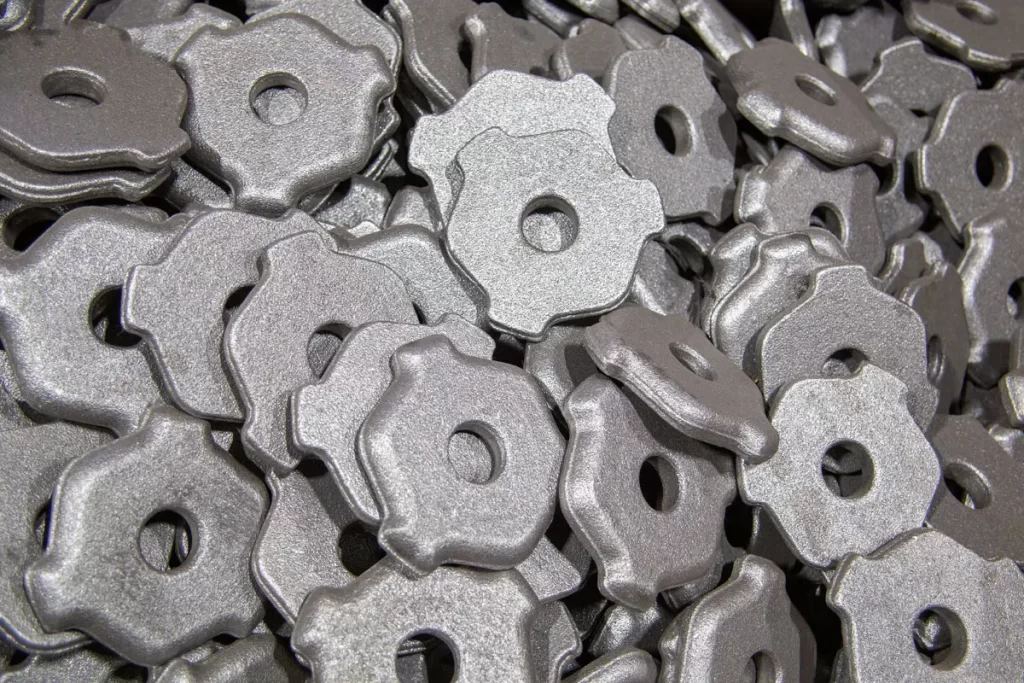
Shilpan Steelcast, one of the leading manufacturers of forging in India, specializes in delivering high-quality forged components tailored to diverse industries. With expertise in both open-die and closed-die drop forging, we offer customized solutions to meet unique project requirements.
Our services go beyond forging—we also provide comprehensive metal manufacturing options, including investment casting, sand casting, shell moulding, die casting, MIM (Metal Injection Molding), and metal stamping. To complement these, our in-house precision machining facility ensures that every forged part achieves unmatched dimensional accuracy and surface finish.
Backed by advanced quality control systems and a commitment to excellence, Shilpan Steelcast stands out as a trusted partner for all your forging and metal manufacturing needs.
Conclusion
Choosing the right forging process—open-die or closed-die—can make a significant impact on the quality, performance, and cost of your project. While open-die forging excels in producing large, durable components, closed-die forging is ideal for precision-engineered, mass-produced parts.
Shilpan Steelcast – one of the top forging parts manufacturers in India – combines technical expertise with cutting-edge facilities to provide tailored forging solutions for industries worldwide. Whether you require large custom components or intricate, high-volume parts, our team is ready to deliver.
Explore Shilpan Steelcast’s forging expertise and discover how we can add value to your next project. Contact us today or visit our website to learn more about our open-die and closed-die forging capabilities!