Investment Casting & CNC Machining: A Seamless Path to High-Performance Parts
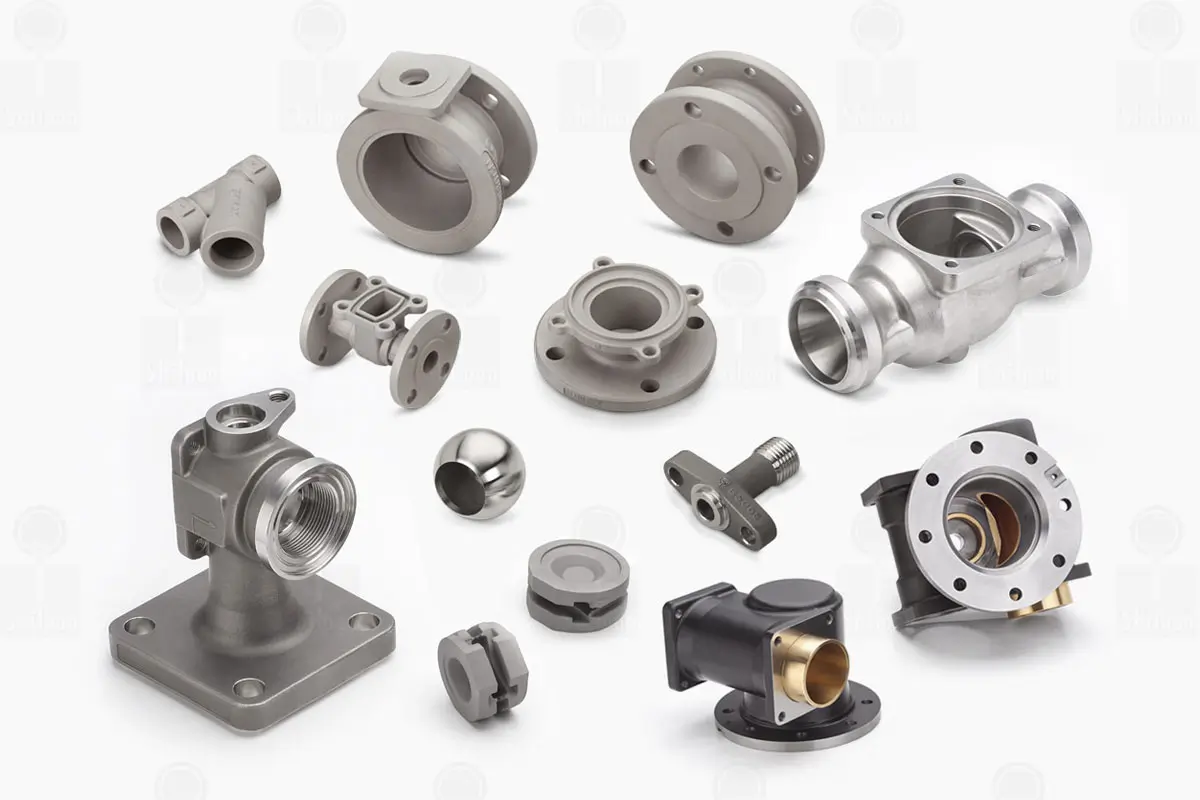
In the modern manufacturing landscape, precision, reliability, and efficiency are more critical than ever. This has led industries to adopt hybrid production strategies that combine the strengths of multiple manufacturing processes. One such powerful combination is investment casting with CNC machining—a synergy that unlocks the potential for highly complex, dimensionally accurate, and high-performance metal components.
At Shilpan Steelcast, this integration isn’t just a convenience—it’s a core capability. With a state-of-the-art in-house CNC machining facility, the company delivers fully finished investment cast parts with unmatched precision and consistency. This article explores why pairing investment casting with CNC machining is a game-changer for modern manufacturing.
Understanding Investment Casting
Investment casting, also known as lost-wax casting, is a precision metal casting process used to create intricate components with tight tolerances, excellent surface finish, and minimal material waste. The process involves creating a wax model, forming a ceramic shell around it, and then casting molten metal into the shell to produce the final component.
Key Benefits of Investment Casting
- Exceptional surface finish
- High dimensional accuracy
- Ability to produce complex geometries
- Material versatility (steel, superalloys, stainless steel, etc.)
- Minimal post-processing in many cases
Industries such as aerospace, automotive, defense, oil & gas, and industrial machinery rely heavily on investment casting for mission-critical parts that demand reliability and precision.
CNC Machining: Precision Redefined
CNC (Computer Numerical Control) machining is a subtractive manufacturing process where material is removed from a solid block or casting using computer-controlled cutting tools. CNC machining is known for its ability to achieve ultra-high precision and tight tolerances that are difficult to match with casting alone.
Why CNC Machining is Important after Investment Casting
- Final finishing to achieve tight tolerances
- Creating threaded holes or intricate slots
- Removing any remaining surface irregularities
- Achieving perfectly flat or cylindrical surfaces
- Enhancing dimensional stability
When combined with investment casting, CNC machining refines and perfects the component, resulting in ready-to-install parts that meet the most demanding specifications.
How Investment Casting and CNC Machining Complement Each Other
While investment casting creates near-net-shape components, CNC machining brings these components to their final dimensions. Here’s how the combination offers superior value:
- Design Flexibility: Intricate internal and external geometries can be achieved through casting, while fine details and critical fits are ensured by machining.
- Cost Efficiency: Casting reduces material waste and machining time, especially for complex parts.
- Superior Quality: The combined process ensures an enhanced surface finish, dimensional accuracy, and performance.
- Lead Time Reduction: Integrating both processes in-house allows for faster turnaround and fewer outsourcing delays.
This seamless combination is especially valuable in industries where performance and precision cannot be compromised—like aerospace components, automotive transmission parts, and medical implants.
Shilpan Steelcast: Your Single-Source Solution for Investment Casting & CNC Machining
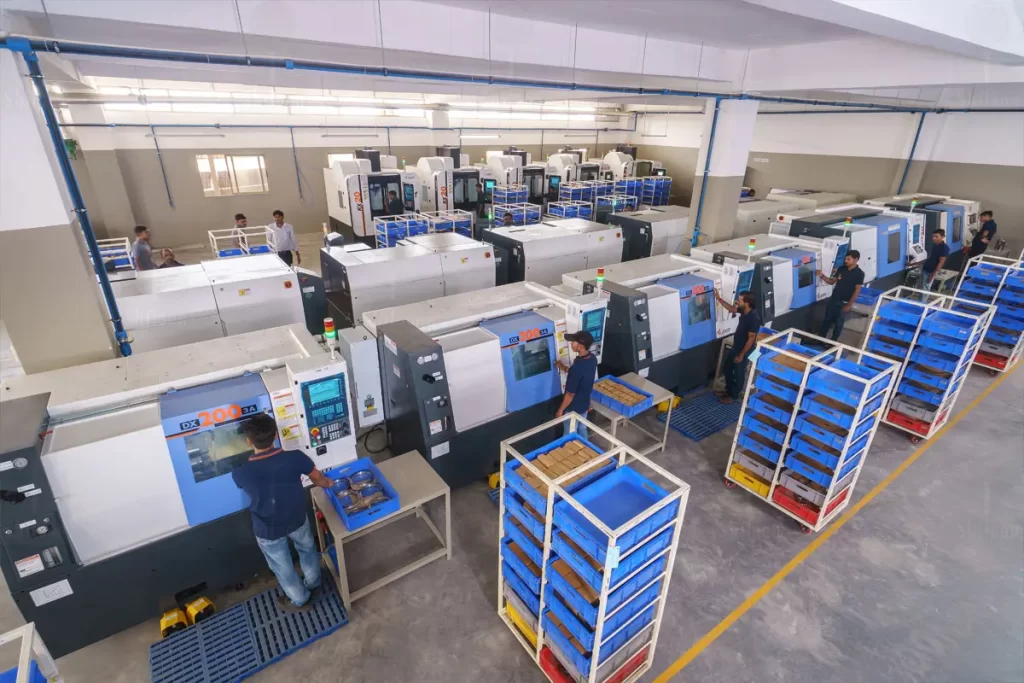
At Shilpan Steelcast, integration is a strategic advantage. The company’s in-house CNC machining facility complements its investment casting foundry, delivering fully finished components that meet the most demanding specifications.
Key In-House Capabilities
- Multi-axis CNC turning and milling machines
- CAD/CAM programming and toolpath optimization
- Dedicated inspection and quality control labs
- Experienced engineers for DFM (Design for Manufacturability) guidance
This integrated setup eliminates the need for third-party machining vendors, reduces logistical overhead, and ensures consistent quality from start to finish.
Advantages of In-House Machining at Shilpan Steelcast
- Faster Turnaround Times: No waiting on external vendors—machining begins as soon as casting is complete.
- Superior Quality Control: Complete oversight across casting and machining leads to better consistency and fewer defects.
- Cost Optimization: Consolidated processes help reduce handling costs, waste, and time.
- Better Communication & Coordination: Seamless flow of information across teams ensures faster problem-solving and improved production flow.
End-to-End Capabilities with Value-Added Assembly Services
To further enhance value and streamline the supply chain for clients, Shilpan Steelcast offers in-house assembly services in addition to investment casting and CNC machining. This enables the delivery of completely assembled, ready-to-use components, significantly reducing the need for multiple vendors or additional processes at the client’s end.
Whether it’s mechanical sub-assemblies, fastening, or integration of multiple cast and machined components, Shilpan’s assembly services are designed to:
- Reduce production time and logistics costs
- Ensure better quality control through unified oversight
- Improve product consistency and performance
- Simplify procurement and vendor management for customers
By offering this extended capability under one roof, Shilpan Steelcast truly becomes a single-source manufacturing partner—from raw casting to finished, assembled products.
Sustainability and Operational Efficiency
Combining casting and machining under one roof isn’t just about speed and precision—it also reduces the environmental impact:
- Lower Carbon Footprint: Eliminates transport between separate suppliers.
- Efficient Material Use: Casting + precise machining means less raw material waste.
- Energy Efficiency: Optimized scheduling and reduced downtime.
Shilpan Steelcast’s investment in sustainable infrastructure—including a 300 MW solar panel park—further supports its commitment to eco-friendly manufacturing practices. This renewable energy initiative not only powers a significant portion of the facility’s operations but also reflects the company’s forward-thinking approach to sustainability.
Conclusion
The integration of investment casting and CNC machining represents a seamless path to producing high-performance, ready-to-use components with precision, cost efficiency, and scalability. By combining these two manufacturing techniques under one roof, Shilpan Steelcast helps customers reduce lead times, improve product quality, and simplify their supply chain.
If you’re looking for a trusted investment casting partner in India with full-service capabilities—including CNC machining and assembly—Shilpan Steelcast is ready to deliver precision at scale.
Looking for a reliable partner for cast and machined components?
Let Shilpan Steelcast help bring your designs to life—accurately, efficiently, and sustainably. Contact us today!